Organic & Thin Film Field Effect Transistor Fabrication Guide
This guide describes the fabrication of evaporation-free OFETs using the Ossila pre-patterned ITO OFET substrates (product codes: S161 & S162). All layers are deposited by solution to enable rapid device testing with a mobility approaching 10-2 cm2/Vs achieved from transistors based on the organic semiconductor P3HT with a PMMA gate insulator and a PEDOT:PSS gate electrode.
This guide is intended for users familiar with organic electronics and as such for brevity we have used many of the common acronyms without explanation. However, a list of acronyms is available at the back of this guide alongside the molecular structures of materials used.
Process chemicals and consumables required
- Hellmanex III
- Pre-patterned ITO OFET substrates
- PEDOT:PSS (PH1000 PEDOT:PSS)
- 0.45 µm PES and 0.45 μm PTFE (hydrophobic) filters
- Solvent resistant syringes
- Micro-precision cleaning swab
- Isopropyl alcohol
- Hot water
- Encapsulation epoxy
- Glass coverslips
- Micropipette Tips
Processing equipment required/used
- Polypropylene cleaning beaker (C191)
- Substrate rack (E101)
- Hot-plate held at 70°C for solutions
- Hot plate held at 90°C for substrates
- Ossila Spin Coater
- Ultra-sonic bath
- Glass-beaker for Hellmanex solution
- Tweezers (C121)
- Compressed nitrogen gun to dry substrates
- Variable volume micropipette (C2001V2)
Video Guide
Watch the accompanying fabrication video to see the process in action.
Introduction
The Ossila pre-patterned OFET substrates have been designed to enable the fabrication and characterisation of transistors without the need for vacuum evaporation systems or probe stations. This allows devices to be produced and tested with significantly increased speed and simplicity, and makes the system ideal for high throughput material screening experiments as well as teaching and training purposes.
The pre-patterned OFET substrates consist of interdigitated ITO fingers to act as the source-drain contacts and have overall channel dimensions of 30 mm x 50 µm. These relatively large channels mean that contact effects are minimised, so matching the energy levels of the organic semiconductor and contacts become less important. As such the intrinsic Poole–Frenkel (bulk) limited mobility of a material can be more easily assessed independent of contact effects. The 30 mm channel length also has the additional benefit of producing larger currents, making testing and measurement quicker and requiring less sensitive (less expensive) equipment.
The substrate itself is made of high-quality soda-lime float glass with a 20 nm coating of SiO2 (synthetic quartz) which allows for HMDS and OTS treatments to improve mobility. The transparent nature of the ITO/glass also means that opto-electric experiments can be done with ease.
Transistors can be fabricated simply by depositing an organic semiconductor, gate insulator and gate on the substrates (see diagram below for device schematic). By using a synthetic metal deposited from solution for the gate, it is possible to make fully-functioning OFETs by solution processing alone -- thus eliminating the need for vacuum evaporation processes. The use of the Ossila OFET test board also means that devices can be measured at the flick of a switch without the need for expensive probe stations.
In the fabrication example below, the materials are all processed from solution with P3HT used as the organic semiconductor, PMMA as the gate insulator and PEDOT:PSS as the gate. As such, transistors can be fabricated in a matter of minutes once solutions have been prepared and the substrates have been cleaned.
However, while this guide details solution based deposition processes, the substrates are designed to work with a wide variety of different material systems and deposition techniques. Vacuum deposited semiconductors, gate insulators and gate electrodes, can also be used with the appropriate shadow masks also available from Ossila.
Cleaning
The starting point for any high-performance device is always a pristine, clean surface, so careful consideration must be paid to the cleaning routine. While the substrates are supplied wrapped in clean-room tissue, we still recommend a thorough cleaning routine in order to ensure the surfaces are well prepared for the deposition of organic materials.
Here the substrates have been cleaned with a combination of a high performance electronic-grade cleaning agent and immersion in sodium hydroxide (NaOH). The NaOH treatment is used to modify the surface by addition of OH- groups and provide a hydrophilic interface without the need for plasma cleaning (note that certain material/solvent combinations that are particularly close to the wetting envelope will still benefit from a plasma or UV-ozone clean).
For a high-performance electro-optical cleaning agent we recommend the use of Hellmanex III as this provides excellent cleaning performance without leaving a residue on the surface. For the sodium hydroxide solution we typically make a stock solution of 10% by weight in water.
To make cleaning faster and easier, we generally clean substrates in batches using a substrate rack. The use of a substrate rack also has the additional benefits of preventing substrates from scratching each other and enhances cleaning by keeping them vertical so that particulates naturally fall off.
When loading a substrate rack, arrange the substrates so that they all have the same orientation as it is easier to identify the top (ITO) side at this stage. To identify the ITO side, simply look at the edge of the substrate at an oblique angle; the ITO should be seen to go all the way to the edge when facing towards the viewer. This is most obvious when reflecting a light source and so getting the correct positioning of light, substrate and eye makes this task much quicker.
It is also important when handling the substrates to use tweezers at all times, and to handle them by the corners to avoid scratching or contaminating the main body of the substrate.


The exact cleaning routine will depend upon the equipment that is available (make and model of ultrasonic bath) as well as the concentration and temperature of solutions, however the routine below should provide a good base point. The ultrasonic bath should be filled with boiling water to provide hot sonication for both the Hellmanex and the NaOH, reducing cleaning times and improving the performance of the cleaning solutions.
Note: Always take additional care when handling acid/bases especially when hot and always file appropriate risk assessments with your departmental safety officer before undertaking work. MSDS sheets are available from Ossila.com.
Summary of cleaning routine:
- Sonicate in hot 10% NaOH for 5 minutes.
- Dump rinses (hot water, hot water)
- Sonicate in hot 2% Hellmanex for 5 minutes.
- Dump rinses (hot water, hot water, cold DI water)
- Sonicate in IPA (cold) for 5 minutes
- Blow dry using dry nitrogen
Note that after both the Hellmanex and NaOH treatments the substrates are "dump rinsed" to remove the cleaning agent. This consists of placing them in three successive beakers of water, the first two of which contain boiling water and the third one de-ionised (DI) water. Note that while DI water can be used for all stages of cleaning we have found no evidence of doping of the active layer (or other changes in performance) when using normal water although this could vary depending upon the location and ionic content of the water (hard/soft water). For the sake of caution we usually use DI water as the final dump rinse.
Fabrication
OFETs were fabricated in a bottom-contact top-gate configuration with the following layers spun sequentially.
- Surface treatment (HMDS)
- Organic semiconductor (P3HT)
- Gate insulator (PMMA)
- Gate electrode (PEDOT:PSS)
Surface Treatments
Surface treatments are important to obtain high mobilities from P3HT OFETs, therefore, a spin-coated HMDS surface treatment was used prior to P3HT deposition. However, vapour phase HMDS or liquid phase OTS treatments are also possible. There are many procedures used in the literature, but if you would like more information about surface treatments please contact our experts.
Active Layer
In the example devices shown here, P3HT has been used as the organic semiconductor, but this process is compatible with most polymeric semiconductors such as PCDTBT and PBTTT. In order to maximise the performance of the P3HT, we have used the high boiling-point solvent 1,2,4-Trichlorobenzene (TCB) in conjunction with a medium molecular weight P3HT (Ossila M107, Mw = 24,480 kDa). The P3HT was dissolved in the TCB at 10 mg/ml on a hotplate at 80°C for 30 minutes with stirbar (1000 rpm) before being left to cool to room temperature over 10 minutes and filtered with a 0.45 μm PTFE (hydrophobic) membrane filter.
Gate Insulator
The use of sequential spin-cast layers means that the choice of gate dielectric and its corresponding solvent are also critical and an orthogonal solvent system is required to ensure that the active semiconductor is not washed away when the gate dielectric is deposited.
For most polymeric semiconductors, a gate dielectric of PMMA dissolved in butan-2-one will fulfil the required parameters. The molecular weight of the PMMA is important because a thick uniform film is required. We use a PMMA with a molecular weight of 120,000 and dissolve it at 100 mg/ml in butan-2-one in order to provide the thickest possible films and reduce gate leakage. Molecular weights significantly higher than this can cause solubility issues and uneven films while significantly. Molecular weights lower than this can cause pin-holes and solvent incompatibility with solution processed gate electrodes. To aid dissolution, the solution was heated for 30 minutes at 80°C and stirred at 1000 rpm before being left to cool to room temperature over 10 minutes and filtered through a 0.45 µm PTFE (hydrophobic) membrane filter.
Processing Conditions
All stages of the organic deposition were performed within a nitrogen glove box. However, when used with suitably stable semiconductors (such as PCDTBT), these steps could also be performed in air.
Different spin coating techniques are used for the various layers, with the most important difference being between a static and dynamic solution-dispensing technique. In a static dispense, the substrate is first covered in solution and then started spinning; in a dynamic dispense the substrate is set spinning (and allowed time to reach the correct spin speed) before the solution is dispensed into the centre of the substrate. To find out more about these techniques, read our Spin Coating Guide
The best spin-coating technique depends upon the wetting properties and viscosity of the solution and the evaporation rate of the solvent among other factors. A static dispense can often give better coverage at spin speeds below 1000 rpm and also give more time for surface interactions which is why this technique was used for the HMDS. Meanwhile a dynamic dispense is often preferable at high spin speeds and for fast-evaporating solvents and uses much less material (at 1000 rpm and above 20 µl is usually sufficient). As such a dynamic dispense was used for the P3HT and PMMA.
When spun from TCB the P3HT also benefits from a two-stage spin due to its high boiling point, and consequently, slow drying time. Typically the first stage is used to dry the film to the desired thickness over the majority of the substrate and a second, much faster, stage is used to dry the corner beads that are still wet after the end of the first stage. Without the second stage, the corners would take an excessively long time to dry or require the solvent to be removed by a cotton bud.
The spin coating regime for the transistors can therefore be summarised below. While the three layers can be applied separately, if a programmable spin-coater is available then all three layers can be applied consecutively without the substrate ever being allowed to stop. This allows for faster fabrication and can also be used to minimise the exposure of the organic semiconductor to air if being spun under ambient conditions.
Spin the HMDS
- Static dispense of 100 µl
- Spn at 2000 rpm for 30 seconds
Spin coat the P3HT
- Dissolved in TCB at 10 mg/ml
- Dynamic dispense of 30 µl
- Spin at 1500 rpm for 150 seconds to dry the active area
- Spin at 4000 rpm for 30 seconds to dry the corner beads.
- Wipe clean the gate and contact pads with cleanroom swab dipped in chlorobenzene
Spin coat the PMMA
- Dissolved in butan-2-one at 100 mg/ml
- Dynamic dispense of 100 µl
- Spin at 1000 rpm for 30 seconds
- Scratch off PMMA from gate and contact pads using precision tweezers
- Bake at 105 °C for 5 mins
Gate Electrode
Following deposition of the gate insulator a conductive gate electrode must be applied. The use of a solution-processed gate enables rapid fabrication without the use of costly and slow vacuum deposition equipment. However, any solution-processed gate also needs to be solvent compatible with the gate insulator (and preferably organic semiconductor as well). It should also have the right wetting and film-forming properties to enable uniform substrate coverage. A high conductivity PEDOT:PSS formulation such as PH1000 can be applied on top of the PMMA if mixed with additives to control the wetting properties. We have found that the following recipe works well for our devices
Component | Order to add | % by weight |
PH1000 PEDOT:PSS | 1 | 42.5 |
N-Methyl-2-pyrrolidone (NMP) | 2 | 2.5 |
Triton X-100 | 3 | 1 |
Isopropyl Alcohol | 4 | 54 |
NMP is a solvent for increasing conductivity to PH1000. Triton X-100 is a surfactant to ensure complete mixing. IPA is used to improve spin coating by improving the repeatability, wettability and drying.
Spin coat PEDOT:PSS mixture
- Spin coat using a 50 µl dynamic dispense at 4000 RPM
- Wipe clean the contact pads using cleanroom swab dipped in IPA
It is important that this solution should make contact with the gate electrode strip, but not the source-drain contacts (see schematic below).
Alternatively, a few drops of the PEDOT:PSS mixture can simply be placed over the electrode areas and left to dry slowly under atmospheric conditions. However this is less repeatable than spin coating the substrates.
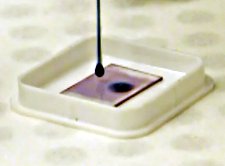
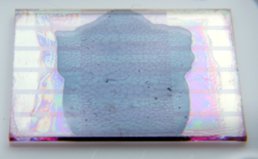
Measurement
The devices were characterised using a dual source-measure unit under computer control. An Ossila test board was used to connect and switch between the individual OFETs on a substrate. In this case, testing was performed under ambient atmosphere in darkness. However, the OFET measurement board is designed to be small enough to fit inside a glove box to enable measurements under an inert atmosphere as well. When testing under ambient conditions, exposure to air and light levels must be minimised. As such, we recommend storing the finished devices in sealed vials until measurement.
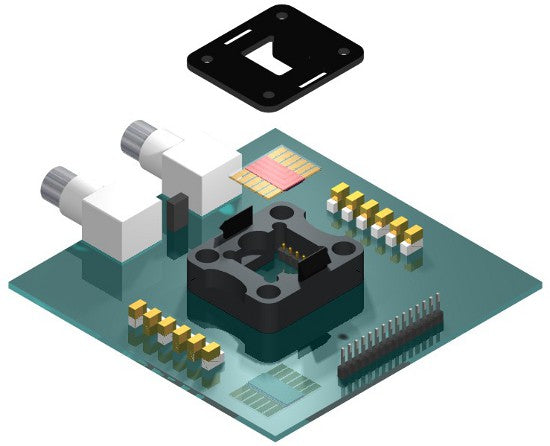
For the output characteristics the drain voltage was swept from +12 V to -40 V for each gate voltage tested from +10 V to -40 V (in -10 V steps); for the transfer characteristics the gate voltage was swept from +12 V to -40 V for each of the two drain voltages tested (-4 V and -40 V). It is recommended that three of each characteristic test is run, to enable the device to “burn-in”.
The data obtained from the device pictured above can be seen below, the device shows good saturation in the output characteristics, while the transfer plot reveals a mobility of 9.26 x 10-3 cm2V-1s-1 and a threshold voltage -2.31 V. This compares with the highest reported values in the literature for P3HT in the region of 10-1 cm2V-1s-1 from devices with vacuum-deposited gold electrodes and typical channel lengths of <25 µm.
Summary
Using the Ossila pre-patterned ITO substrates, it is possible to fabricate transistors using fully solution-based depositions in a bottom contact top-gate configuration and thus avoid the need for vacuum evaporation. The larger channel width and long channel length of the substrates make them ideal for measuring Poole-Frenkel (bulk) limited mobilities, and thus an excellent screening system to compare the intrinsic properties of different materials while minimising injection differences due to the contacts.
The key considerations for successful fabrication are the choice of gate dielectric and solvent.
Acronyms and Molecular Structures
HMDS | Hexamethyldisilazane |
HOMO | Highest occupied molecular orbital |
IPA | Isopropyl alcohol |
ITO | Indium tin oxide |
NaOH | Sodium hydroxide |
NMP | N-Methyl-2-pyrrolidone |
OFET | Organic field effect transistor |
OTS | Octadecyltrichlorosilane |
P3HT | Poly(3-hexylthiophene-2,5-diyl) |
PBTTT | Poly(2,5-bis(3-tetradecylthiophen-2-yl)thieno[3,2-b]thiophene) |
PCDTBT | Poly[N-9'-heptadecanyl-2,7-carbazole-alt-5,5-(4',7'-di-2-thienyl-2',1',3'-benzothiadiazole)] |
PEDOT:PSS | Poly(3,4-ethylenedioxythiophene) poly(styrenesulfonate) |
PES | Polyether sulfone |
PMMA | Poly(methyl methacrylate) |
PTFE | Polytetrafluoroethylene |
RPM | Revolutions per minute |
TCB | 1,2,4-Trichlorobenzene |
PEDOT Polymer Blends

Learn More

The Long Channel Organic Field-Effect Transistor (OFET) source/drain evaporation stack is designed to make fabrication as simple as possible so you can focus on material testing rather than fabrication.
Read more...Organic electrochemical transistors (OECTs) regulate charge flow through an organic semiconductor channel via ion injection from an electrolyte. The most common organic semiconductor used is PEDOT:PSS.
Read more...