Microbalances: A Case Study on Accuracy and Precision
In this case study, we looked at the influence of microbalances on the accuracy and precision of the spin coating process, especially the thickness and evenness of the films it creates. By using a microbalance to measure the solution components, we show the relationship between accurate mass measurements and solution concentration, which lead to uneven films uniformity. It is known that mistakes in weighing will cause changes in concentrations, resulting in varying thickness in coating film. To highlight the effectiveness of the Ossila microbalance, we tested the measurements against a less accurate analytical balance from a competing company. The results showed the critical role of precise measurement in preparing coating solutions, highlighting the importance of using an accurate microbalance in spin coating.
Introduction
Spin coating is a critical process in thin film fabrication, used in various industries such as electronics, material science and photonics. The method typically involves depositing a solution onto a substrate, which is then rotated at high speeds (usually around 3000 rpm) to spread the solution evenly across the substrate (Mitzi et al., 2004). This coating technique is ideal for producing thin, uniform films over a range of sizes. However, whilst achieving the desired film thickness and uniformity is essential, it can pose challenges. It is essential because variations in film thickness can compromise the functional properties of the film; such as electric, optical and mechanical characteristics. In various applications, such as semiconductors and optical coatings, the film must meet precise specifications (often thicknesses must be in the nanometre range). As well as this, spin coating is also a frequent application used in micro-fabrications to produce films with thicknesses under 10 nm. It can be employed in photolithography for applying photoresist layers around 1 μm thick (Hanaor et al., 2011).
One of the crucial factors which influence the spin coating process is the concentration of the coating solution, which has two main affects: the first is through directly impacting the film thickness due to more solute being present once the film has been set and the second is that the viscosity can vary which influences how the film spreads and dries during rotation. Small variations in concentration can lead to significant changes in the film thickness. Therefore, having exact measurements when weighing the mass of solutes is very important to ensure consistency in measurement. This emphasises the usefulness of microbalances, which are precision instruments designed to measure very small masses with high accuracy. In the spin coating technique, microbalances are used to weigh the solutes that will be dissolved in solvents that ultimately form the coating solution.
Microbalances differ from typical analytical balances due to the ability to detect very small mass differences, making them ideal for applications such as weighing of a solute. They are also essential laboratory tools in applications which require high accuracy and precision, particularly in fields such as material science, pharmaceuticals and nanotechnology. In comparison to analytical balances, microbalances offer finer resolution as they can detect smaller changes in mass. This enhanced precision can offer an advantage when working with small sample sizes, as the slightest deviation can have consequences on the outcome of an experiment. The design of a microbalance involves technology which ensures stability and accuracy in measurements. It is important that microbalances can operate in temperature and vibration-controlled environments to minimise the effects of external factors.
The mass of the solute ultimately influences the final coating produced from the spin coater. For example, if the mass of the solute is lower than intended, then the solution becomes less concentrated leading to a thinner film than expected. On the other hand, if the mass of the solute is higher, then the solution will be more concentrated, which leads to a thicker film than expected. The precision of microbalances helps to avoid such errors, allowing for the preparation of highly consistent solutions that produce films with a predictable thickness. As such, microbalances are critical in areas such as electronics, where coating thicknesses need to be within tight measurements to ensure the functionality of the device.
Case Presentation
This case study examines how the accuracy and precision of the Ossila microbalance influences the concentration of a spin coating solution which invariably affects the thickness of the resulting film. To investigate this, various films were prepared through spin coating with coating solutions which had varying concentrations. Each film thickness created was measured using a surface profilometer to quantify how changes in concentration affect the coating results.
For this study, different batches of polymethylmethacrylate (PMMA) dissolved in xylene were prepared and applied to substrates. To measure and compare the accuracy of the microbalance, we also conducted the same experiment using an analytical balance.
The measured concentrations were as follows:
- 10 mg/mL measured using the analytical balance
- 20 mg/mL measured using the analytical balance
- 40 mg/mL measured using the analytical balance
- 4 mg/mL measured using the Ossila microbalance
- 8 mg/mL measured using the Ossila microbalance
- 16 mg/mL measured using the Ossila microbalance
The concentrations were then repeated three times, and an average was taken:
Thickness (nm) |
Thickness (nm) |
Thickness (nm) |
Average thickness (nm) |
Standard Deviation (nm) |
|
10 mg/mL |
20 |
32 |
33 |
30 |
7.23 |
20 mg/mL |
40 |
51 |
29 |
40 |
11 |
40 mg/mL |
71 |
55 |
65 |
63 |
8.08 |
4 mg/mL |
12 |
11 |
8 |
10 |
2.08 |
8 mg/mL |
21 |
25 |
19 |
22 |
3.06 |
16 mg/mL |
54 |
45 |
53 |
51 |
4.93 |
Discussion
The results of the study highlight the importance of accurate weighing when making a smooth and even film in spin coating. There were noticeable differences when comparing the consistency of results between the films created using solutions prepared with an analytical balance (10 mg/mL, 20 mg/mL and 40 mg/mL) to the films created using solutions prepared with a microbalance (4 mg/mL, 8 mg/mL and 16 mg/mL). An important metric used to measure the consistency was the standard deviation values. For the films prepared by the analytical balance, the standard deviation values were quite high: from 7.23 nm to 11 nm. This is a noticeable difference compared to the standard deviations of the microbalance-prepared films which ranged from 2.08 to 4.93. The data shows a greater variability in thickness measurements for the films prepared by the analytical balance. This can be seen by looking at the concentration 20 mg/mL; the measurements were 40 nm, 51 nm and 29 nm. This resulted in an unreliable average of 40 nm, as it was calculated from inconsistent measurements. On the contrary, solutions prepared using the Ossila microbalance showed more consistency and reliability.
These results show that the use of Ossila Microbalance was instrumental in preparing solutions to achieve precise concentrations of PMMA. The weight of PMMA has a big impact in the final film thickness, any inaccuracies in weighing could have led to significant deviations in film thickness. This emphasises the importance of high accuracy and precision when working with thin films that require nanometre scale thickness accuracy. Differences of just 0.1 mg in solute weight can alter the concentration of the solution. The internal calibration feature of the Ossila microbalance supported the overall accuracy of the experiment and reduced possible human error. This helps to ensure the results were reliable and consistent. Despite using a microbalance it is possible for human and technical errors to affect the weighing process, which can disrupt the expected positive relationship between solute concentration and film thickness in spin coating experiments.
Inconsistencies with the spin coating technique can also affect the final thickness of the film. Spin coating requires the coating solution to be dispensed onto the substrate with minimal delay, which helps control any solvent evaporation. If there is variation in the time taken to apply the solution after weighing, the solvent may start evaporating inconsistently as it spreads. This would alter the final concentration. For example, applying the solution using a different amount of force can lead to uneven film distribution, as the solution may spread differently during spinning. Small differences in how the solution is applied each time can affect final thickness that obscure a clear linear relationship. Human delays or inconsistencies in application time can also lead to variations in final film thickness, disturbing the concentration and thickness linearity.
Conclusion
This case study highlights the importance of controlling solute concentration in achieving a consistent film thickness in spin coating applications. By utilising an Ossila Microbalance we were able to prepare coating solutions with controlled solute weights, whilst also demonstrating the impact of small variations in solute concentration and how this alters the coating thickness after spin coating. The experiment’s findings showed that higher concentrations generally increased film thickness. The relationship was not perfect, as errors can be caused by various factors such as human error, slight application inconsistencies and solvent evaporation effects.
In conclusion, the spin coater relies on accurate solution properties to apply uniform films across the substrate. Any discrepancies in solute weight will affect this uniformity, leading to variances in the final film thickness. Therefore, the Ossila microbalance acts as a foundational piece of equipment, enabling the spin coater technique to be carried out effectively.
Microbalance
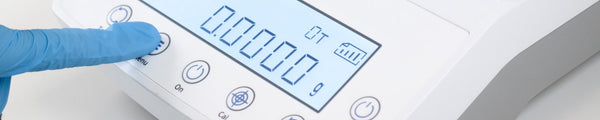
Learn More

The instructions in the video and below describe how to correctly use a laboratory balance. Following this method will prolong the working life of your laboratory balance and keep it weighing as accurately as possible.
Read more...
Spin coating is a common technique for applying thin films to substrates. When a solution of a material and a solvent is spun at high speeds, the centripetal force and the surface tension of the liquid together create an even covering.
Read more...References
- Tyona, M.D. A theoritical study on spin coating technique Advances in materials Research, 2(4), p.195., 2013
- Mitzi, D.B., Kosbar, L.L., Murray, C.E., Copel, M. and Afzali, A. High-mobility ultrathin semiconducting films prepared by spin coating Nature, 428(6980), pp.299-303, 2004
- 3. Hanaor, D.A.H., Triani, G. and Sorrell, C.C. Morphology and photocatalytic activity of highly oriented mixed phase titanium dioxide thin films Surface and coatings technology, 205(12), pp.3658-3664, 2011
Contributing Authors
Written by
Product Specialist
Edited by
Scientific Writer