Solar Cell I-V Test System User Manual
Contents
- Overview
- EU Declaration of Conformity (DoC)
- Safety
- Warning
- Use of Equipment
- Hazard Icons
- General Hazards
- Power Cord Safety
- Servicing
- Health and Safety - Servicing
- Requirements
- Unpacking
- Specifications
- System Components
- Installation
- Operation
- Measurement Types
- Quick Start Guide
- Shared Software Settings
- Characterisation Settings
- Lifetime Settings
- Stabilised Current Settings
- Saving and Loading Settings
- Saving Results
- Controls
- Plot Controls
- Test Devices
- Troubleshooting
Solar Cell I-V Test System
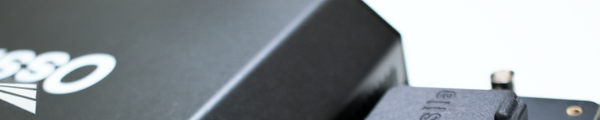
1. Overview
The Ossila Solar Cell I-V Test System is a low-cost solution for reliable current-voltage characterisation of solar cells. The system is controlled by specially designed software which can perform multiple I-V measurements, determine key metrics of solar cells, and measure these properties over long periods of time. The automated version of the system enables automatic switching between pixels, making measurements faster and easier.
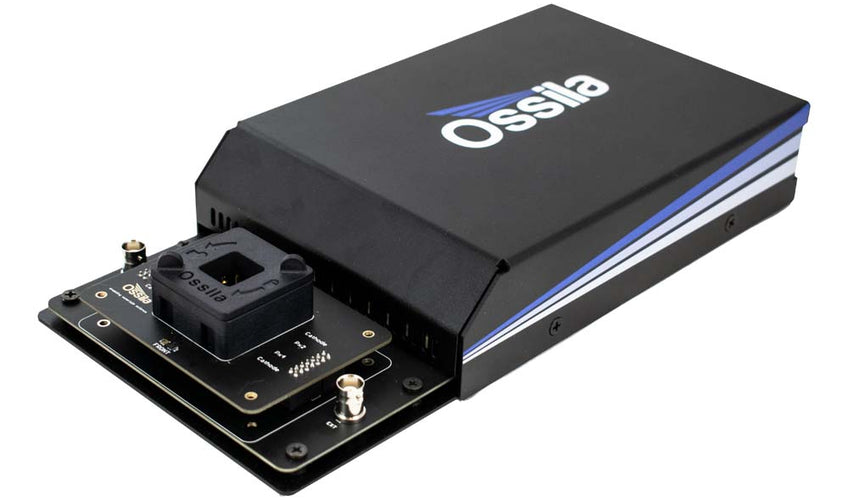
2. EU Declaration of Conformity (DoC)
We
Company Name: Ossila BV
Postal Address: Biopartner 3 Building, Galileiweg 8
Postcode: 2333 BD Leiden
Country: The Netherlands
Telephone Number: +31 (0)718 081020
Email Address: info@ossila.com
declare that the DoC is issued under our sole responsibility and belongs to the following product:
Product: Solar Cell I-V Test System - Manual (T2002A2/T2002B2/T2002D2/T2002E2/T2002F2/T2002G2), Solar Cell I-V Test System – Automated (T2003A3/T2003B3/T2003C3/T2003E3/T2003F3/T2003G3)
Serial Number: T2002A2 - xxxx, T2002B2 - xxxx, T2002D2 - xxxx, T2002E2 - xxxx, T2002F2 - xxxx, T2003A3 - xxxx, T2003B3 - xxxx, T2003C3 - xxxx, T2003E3 - xxxx, T2003F3 - xxxx, T2003G3 - xxxx.
Object of Declaration
Solar Cell I-V Test System – Manual (T2002A2/T2002B2/T2002D2/T2002E2/T2002F2/T2002G2), Solar Cell I-V Test System – Automated (T2003A3/T2003B3/T2003C3/T2003E3/T2003F3/T2003G3)
The object of declaration described above is in conformity with the relevant Union harmonisation legislation:
EMC Directive 2014/30/EU
RoHS Directive 2011/65/EU
Signed:
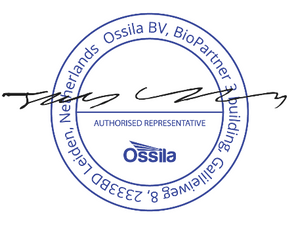
Name: Dr James Kingsley
Place: Leiden
Date: 16/11/2021
Декларация | за съответствие на ЕС |
---|---|
Производител | Ossila BV, Biopartner 3 building, Galileiweg 8, 2333 BD Leiden, NL. |
Декларира с цялата си отговорност, че посоченото оборудване съответства на приложимото законодателство на ЕС за хармонизиране, посочено на предходната(-ите) страница(-и) на настоящия документ. |
[Čeština] | Prohlášení o shodě EU |
---|---|
Výrobce | Ossila BV, Biopartner 3 building, Galileiweg 8, 2333 BD Leiden, NL. |
Prohlašujeme na vlastní odpovědnost, že uvedené zařízeni je v souladu s příslušnými harmonizačními předpisy EU uvedenými na předchozích stranách tohoto dokumentu. |
[Dansk] | EU-overensstemme lseserklærin g |
---|---|
Producent | Ossila BV, Biopartner 3 building, Galileiweg 8, 2333 BD Leiden, NL. |
Erklærer herved, at vi alene er ansvarlige for, at det nævnte udstyr er i overensstemmelse med den relevante EUharmoniseringslovgivning, der er anført på den/de foregående side(r) i dette dokument. |
[Deutsch] | EU-Konformitätserklärung |
---|---|
Hersteller | Ossila BV, Biopartner 3 building, Galileiweg 8, 2333 BD Leiden, NL. |
Wir erklären in alleiniger Verantwortung, dass das aufgeführte Gerät konform mit der relevanten EUHarmonisierungsgesetzgebung auf den vorangegangenen Seiten dieses Dokuments ist. |
[Eesti keel] | ELi vastavusavaldus |
---|---|
Tootja | Ossila BV, Biopartner 3 building, Galileiweg 8, 2333 BD Leiden, NL. |
Kinnitame oma ainuvastutusel, et loetletud seadmed on kooskõlas antud dokumendi eelmisel lehelküljel / eelmistel lehekülgedel ära toodud asjaomaste ELi ühtlustamise õigusaktidega. |
[Ελληνικά] | Δήλωση πιστότητας ΕΕ |
---|---|
Κατασκευαστής | Ossila BV, Biopartner 3 building, Galileiweg 8, 2333 BD Leiden, NL. |
Δηλώνουμε υπεύθυνα όn ο αναφερόμενος εξοπλισμός συμμορφώνεται με τη σχεnκή νομοθεσία εναρμόνισης της ΕΕ που υπάρχει σnς προηγούμενες σελίδες του παρόντος εγγράφου. |
[Español] | Declaración de conformidad UE |
---|---|
Fabricante | Ossila BV, Biopartner 3 building, Galileiweg 8, 2333 BD Leiden, NL. |
Declaramos bajo nuestra única responsabilidad que el siguiente producto se ajusta a la pertinente legislación de armonización de la UE enumerada en las páginas anteriores de este documento. |
[Français] | Déclaration de conformité UE |
---|---|
Fabricant | Ossila BV, Biopartner 3 building, Galileiweg 8, 2333 BD Leiden, NL. |
Déclarons sous notre seule responsabilité que le matériel mentionné est conforme à la législation en vigueur de l'UE présentée sur la/les page(s) précédente(s) de ce document. |
[Hrvatski] | E.U izjava o sukladnosti |
---|---|
Proizvođač | Ossila BV, Biopartner 3 building, Galileiweg 8, 2333 BD Leiden, NL. |
Izjavljujemo na vlastitu odgovornost da je navedena oprema sukladna s mjerodavnim zakonodavstvom EU-a o usklađivanju koje je navedeno na prethodnoj(nim) stranici(ama) ovoga dokumenta. |
[Italiano] | Dichiarazione di conformità UE |
---|---|
Produttore | Ossila BV, Biopartner 3 building, Galileiweg 8, 2333 BD Leiden, NL. |
Si dichiara sotto la propria personale responsabilità che l'apparecchiatura in elenco è conforme alla normativa di armonizzazione UE rilevante indicata nelle pagine precedenti del presente documento. |
[Latviešu] | ES atbils tības deklarācija |
---|---|
Ražotājs | Ossila BV, Biopartner 3 building, Galileiweg 8, 2333 BD Leiden, NL. |
Ar pilnu atbilclību paziņojam, ka uzskaitītais aprīkojums atbilst attiecīgajiem ES saskaņošanas tiesību aktiem, kas minēti iepriekšējās šī dokumenta lapās. |
[Lietuvių k.] | ES atitikties deklaracija |
---|---|
Gamintojas | Ossila BV, Biopartner 3 building, Galileiweg 8, 2333 BD Leiden, NL. |
atsakingai pareiškia, kad išvardinta įranga atitinka aktualius ES harmonizavimo teisės aktus, nurodytus ankstesniuose šio dokumento |
[Magyar] | EU-s megfelelőségi nyilatkozat |
---|---|
Gyártó | Ossila BV, Biopartner 3 building, Galileiweg 8, 2333 BD Leiden, NL. |
Kizárólagos felelösségünk mellett kijelentjük, hogy a felsorolt eszköz megfelel az ezen dokumentum előző oldalán/oldalain található EU-s összehangolt jogszabályok vonatkozó rendelkezéseinek. |
[Nederlands] | EU-Conformiteitsverklaring |
---|---|
Fabrikant | Ossila BV, Biopartner 3 building, Galileiweg 8, 2333 BD Leiden, NL. |
Verklaart onder onze uitsluitende verantwoordelijkheid dat de vermelde apparatuur in overeenstemming is met de relevante harmonisatiewetgeving van de EU op de vorige pagina('s) van dit document. |
[Norsk] | EU-samsvarserklæ ring |
---|---|
Produsent | Ossila BV, Biopartner 3 building, Galileiweg 8, 2333 BD Leiden, NL. |
Erklærer under vårt eneansvar at utstyret oppført er i overholdelse med relevant EU-harmoniseringslavverk som står på de(n) forrige siden(e) i dette dokumentet. |
[Polski] | Deklaracja zgodności Unii Europejskiej |
---|---|
Producent | Ossila BV, Biopartner 3 building, Galileiweg 8, 2333 BD Leiden, NL. |
Oświadczamy na własną odpowiedzialność, że podane urządzenie jest zgodne ze stosownymi przepisami harmonizacyjnymi Unii Europejskiej, które przedstawiono na poprzednich stronach niniejszego dokumentu. |
[Por tuguês] | Declaração de Conformidade UE |
---|---|
Fabricante | Ossila BV, Biopartner 3 building, Galileiweg 8, 2333 BD Leiden, NL. |
Declara sob sua exclusiva responsabilidade que o equipamento indicado está em conformidade com a legislação de harmonização relevante da UE mencionada na(s) página(s) anterior(es) deste documento. |
[Română] | Declaraţie de conformitate UE |
---|---|
Producător | Ossila BV, Biopartner 3 building, Galileiweg 8, 2333 BD Leiden, NL. |
Declară pe proprie răspundere că echipamentul prezentat este în conformitate cu prevederile legislaţiei UE de armonizare aplicabile prezentate la pagina/paginile anterioare a/ale acestui document. |
[Slovensky] | Vyhlásenie o zhode pre EÚ |
---|---|
Výrobca | Ossila BV, Biopartner 3 building, Galileiweg 8, 2333 BD Leiden, NL. |
Na vlastnú zodpovednosť prehlasuje, že uvedené zariadenie je v súlade s príslušnými právnymi predpismi EÚ o harmonizácii uvedenými na predchádzajúcich stranách tohto dokumentu. |
[Slovenščina] | Izjava EU o skladnosti |
---|---|
Proizvajalec | Ossila BV, Biopartner 3 building, Galileiweg 8, 2333 BD Leiden, NL. |
s polno odgovornostjo izjavlja, da je navedena oprema skladna z veljavno uskladitveno zakonodajo EU, navedeno na prejšnji strani/prejšnjih straneh tega dokumenta. |
[Suomi] | EU-vaatimustenm ukaisuusvakuutus |
---|---|
Valmistaja | Ossila BV, Biopartner 3 building, Galileiweg 8, 2333 BD Leiden, NL. |
Vakuutamme täten olevamme yksin vastuussa siitä, että tässä asiakirjassa luetellut laitteet ovat tämän asiakirjan sivuilla edellisillä sivuilla kuvattujen olennaisten yhdenmukaistamista koskevien EU-säädösten vaatimusten mukaisia. |
[Svenska] | EU-försäkran om överensstämmelse |
---|---|
Tillverkare | Ossila BV, Biopartner 3 building, Galileiweg 8, 2333 BD Leiden, NL. |
Vi intygar härmed att den utrustning som förtecknas överensstämmer med relevanta förordningar gällande EUharmonisering som fmns på föregående |
3. Safety
3.1 Warning
- Do NOT connect external voltage sources to either SMU channel.
- The absolute maximum input voltage for the Vsense channels is ±12 V. Do NOT apply input while not powered.
3.2 Use of Equipment
The Ossila Solar Cell I-V Test System is designed to be used as instructed. It is intended for use under the following conditions:
- Indoors in a laboratory environment (pollution degree 2).
- Altitudes up to 2000 m.
- Temperatures of 5°C to 40°C; maximum relative humidity of 80% up to 31°C.
The unit is supplied with a 24 VDC power adapter with a power cord for the country of purchase, in accordance with European Commission regulations and British Standards. Use of any other electrical power cables, adaptors, or transformers is not recommended.
3.3 Hazard Icons
The following symbols can be found at points throughout the rest of the manual. Note and read each warning before attempting any associated operations associated with it:
Table 3.1 Hazard warning labels used in this manual.
Symbol | Associated Hazard |
---|---|
![]() |
Electrical shock |
3.4 General Hazards
Before installing or operating the Ossila Solar Cell I-V Test System there are several health and safety precautions which must be followed and executed to ensure safe installation and operation.
3.5 Power Cord Safety

Emergency power disconnect options: use the power cord as a disconnecting method and remove from wall. To facilitate disconnect, make sure the power outlet for this cord is readily accessible to the operator.
3.6 Servicing
If servicing is required, please return the unit to Ossila Ltd. The warranty will be invalidated if:
- Modification or service has taken place by anyone other than an Ossila engineer.
- The Unit has been subjected to chemical damage through improper use.
- The Unit has been operated outside the usage parameters stated in the user documentation associated with the Unit.
- The Unit has been rendered inoperable through accident, misuse, contamination, improper maintenance, modification, or other external causes.
3.7 Health and Safety - Servicing

Servicing should only be performed by an Ossila engineer. Any modification or alteration may damage the equipment, cause injury, or death. It will also void your equipment’s warranty.
4. Requirements
Table 4.1 details the power requirements for the Solar Cell I-V Test System, and the minimum computer specifications for the Ossila Solar Cell I-V software.
Table 4.1 Solar Cell I-V Test System requirements.
Power | 24 VDC |
---|---|
Operating Systems | Windows 10 or 11 (64-bit) |
CPU | Dual Core 2 GHz |
RAM | 4 GB |
Available Hard Disk Space | 241 MB |
Monitor Resolution | 1680 x 1050 |
Connectivity |
USB 2.0 Ethernet (requires DHCP) |
5. Unpacking
5.1 Packing List
The standard items included with the Ossila Solar Cell I-V Test System are:
- Ossila Solar Cell I-V Test System.
- 24 VDC power adapter.
- USB-B cable.
- USB memory stick pre-loaded with the user manual, USB drivers, quality control data, and software installer.
- Resistor test device.
5.2 Damage Inspection
Examine the components for evidence of shipping damage. If damage has occurred, please contact Ossila directly for further action. The shipping packaging will come with a shock indicator to show if there has been any mishandling of the package during transportation.
6. Specifications
The Solar Cell I-V Test System specifications are shown in Table 6.1.
Table 6.1 Ossila Solar Cell I-V Test System specifications.
Voltage range | ±10 mV to ±10 V |
---|---|
Voltage accuracy | ±10 mV offset |
Voltage resolution | 170 μV |
Current range | ±10 nA to ±200 mA (5 ranges) |
Current accuracy | ±10 nA (at 20 μA range) |
Current resolution | 0.1 nA (at 20 μA range) |
Substrate Size |
20 mm x 15 mm 25 mm x 25 mm 75 mm x 25 mm |
Substrate Compatibility |
T2002B, T2003B - ITO Glass Substrates (S211) T2002E, T2003E - Patterned ITO Glass Substrates, Unpatterned ITO Glass Substrates, Ultra-flat Quartz Coated Glass Substrates T2002F, T2003F - Pixelated or Module Design ITO Glass Substrates |
Overall Dimensions (Automated) |
Width: 150 mm Height: 55 mm Depth: 300 mm |
Overall Dimensions (Manual) |
Source Measure Unit Width: 125 mm Height: 55 mm Depth: 185 mm |
Test Board (T2002B/T2002E) Width: 105 mm Height: 40 mm Depth: 125 mm |
|
T2002F Width: 100 mm Height: 40 mm Depth: 150 mm |
7. System Components
The Solar Cell I-V Test System is comprised of 2 items: the Solar Cell I-V Test System (Figure 7.1 or Figure 7.2) and the Ossila I-V Curve software (Figure 7.3).
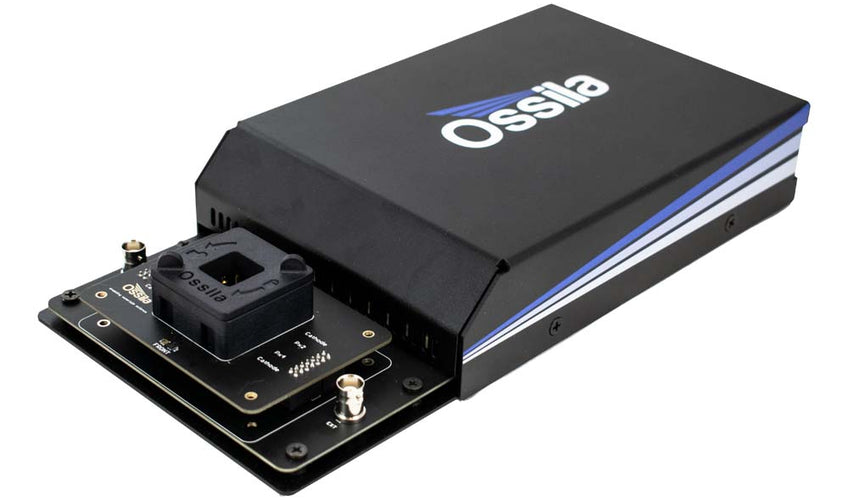
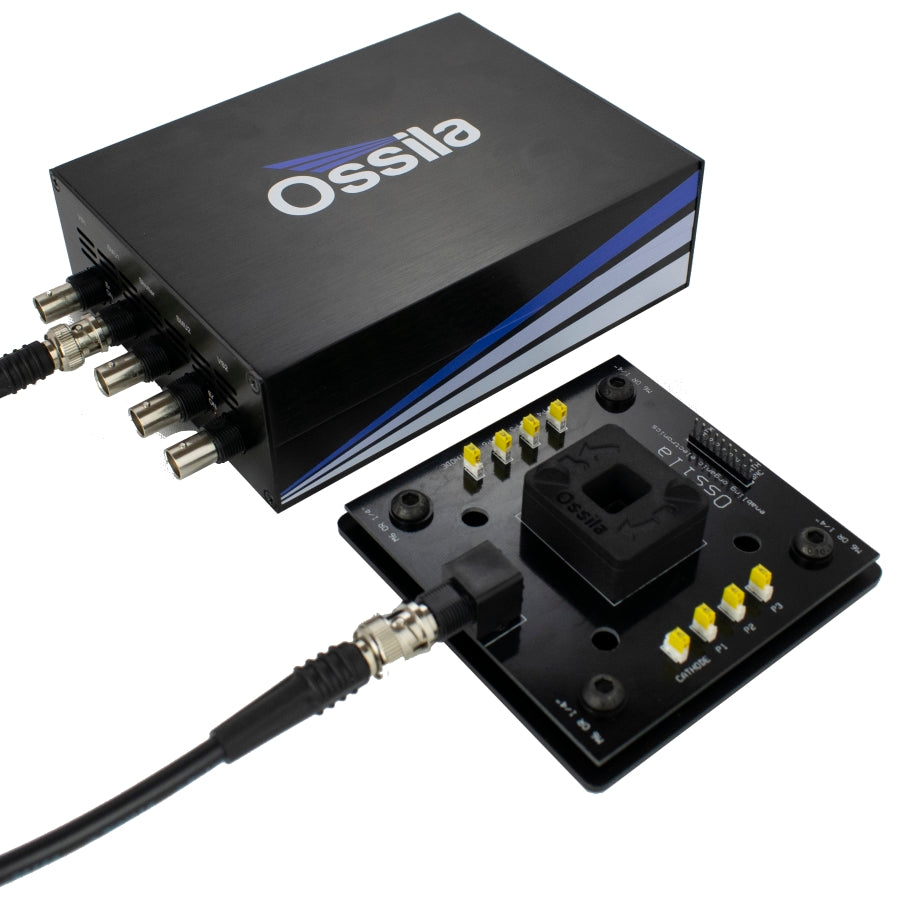
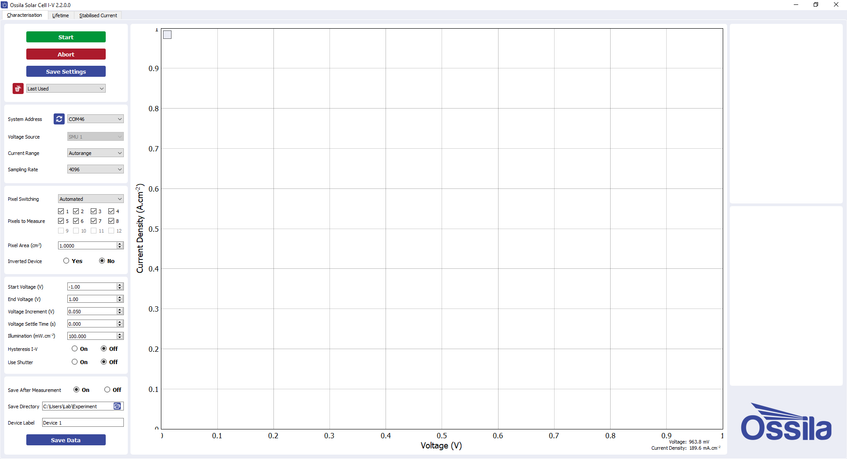
8. Installation
- Install the Ossila Solar Cell I-V software on your PC. Run the file ‘Ossila-Solar-Cell-IV-Installer-vX-X-X-X.exe’ on the USB memory stick provided. Follow the on-screen instructions to install the software.
- Connect the 24 VDC power adaptor to the power socket on the rear of the unit.
- Connect the unit to your PC using the provided USB-B cable, or an Ethernet cable if preferred.
9. Operation
9.1 Measurement Types
The Solar Cell I-V software can perform 3 different types of measurements. Each measurement type can be selected using the tabs at the top of the window. The available measurements are:
- Characterisation (Section 9.1.1).
- Lifetime (Section 9.1.2).
- Stabilised Current (Section 9.1.3).
Each measurement type requires several settings to be selected before it can be performed. Settings that are shared between all measurements are detailed in Section 9.3. Measurement specific settings are detailed in Sections 9.4, 9.5, and 9.6.
9.1.1 Characterisation
The Characterisation tab performs current-voltage (I-V) measurement and analysis of solar cells. The analysis calculates the following properties:
- Power conversion efficiency (PCE)
- Fill factor (FF)
- Short-circuit current density (Jsc)
- Open-circuit voltage (Voc)
- Shunt resistance (Rsh)
- Series resistance (Rs)
- Maximum power (Pmax)
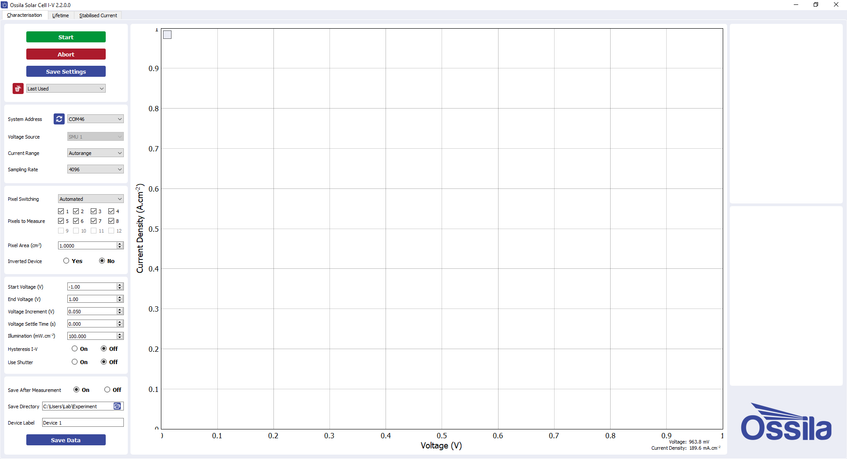
9.1.2 Lifetime
The Lifetime tab tracks PCE, FF, Jsc, and Voc over time by performing periodic I-V measurements and analysis. Between I-V measurements, the solar cell can be held at short-circuit, open-circuit, or maximum power.
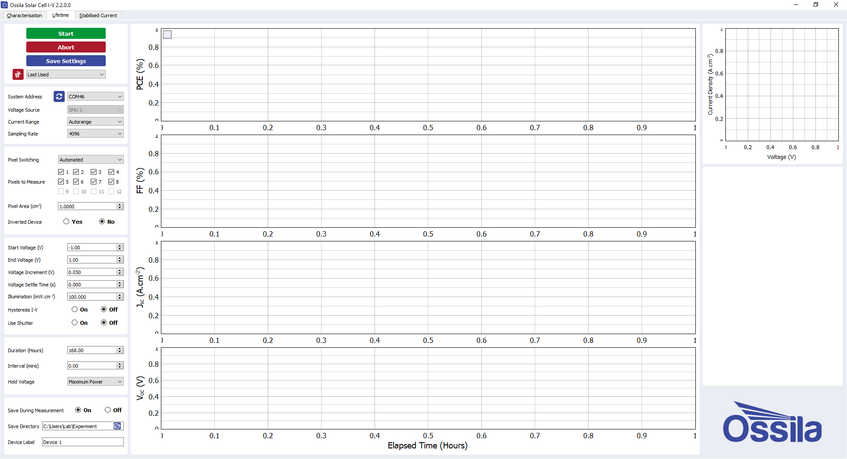
9.1.3 Stabilised Current
The Stabilised Current tab lets you measure the evolution of the photogenerated current at specific voltages.
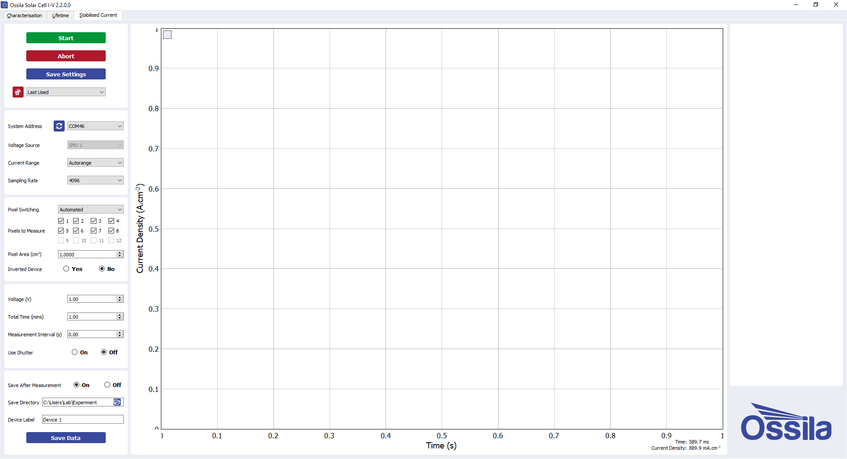
9.2 Quick Start Guide
- Start the Ossila Solar Cell I-V software. The window shown in Figure 9.1 will open.
- Choose a measurement type as described in Section 9.1.
- Place your sample in the device holder.
- Place the device holder beneath your solar simulator.
- Set the appropriate settings in the software (explained in more detail in Sections 9.4 - 9.8).
- Open the shutter of your solar simulator.
- Click the ‘Measure’ button. For each pixel, measurements are performed using the chosen measurement settings. This process is repeated until all pixels have been measured.
- If automatic saving is turned on, the measurement data and settings will then be saved.
9.3 Shared Software Settings
The settings in these sections are shared between all measurement types.
9.3.1 System Settings
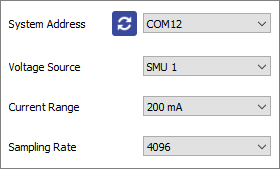
(I) System Address
Select the COM port or IP address of the connected unit you intend to use (USB and Ethernet connection respectively). This box will be populated automatically with the addresses of any units connected to the computer.
(II) Voltage Source
Select which SMU channel of the Source Measure Unit the test board is connected to. ‘SMU 1’ will be automatically selected when pixel switching is set to ‘Automated’.
(III) Current Range
Select the range of currents to be used for the measurement. This defines the upper limit and accuracy of current measurements that can be performed by the unit. The values for each range are given in Table 9.1.
Automatic range selection will start on the lowest current range and automatically switch to higher ranges if the current increases above the maximum for a range.
Table 9.1 Maximum current and accuracy for the current ranges of the Ossila Solar Cell I-V Test System.
Maximum Current | Accuracy | Precision | Resolution |
---|---|---|---|
±200 mA | ±500 μA | 10 μA | 1 μA |
±20 mA | ±10 μA | 1 μA | 100 nA |
±2000 μA | ±1 μA | 100 nA | 10 nA |
±200 μA | ±100 nA | 10 nA | 1 nA |
±20 μA | ±10 nA | 1 nA | 100 pA |
(IV) Sampling Rate
Select the number of samples to be taken for each data point. A higher number of samples per point will improve the accuracy and precision of the measurement. However, this will increase the time taken for the measurement to be performed.
9.3.2 Device Details

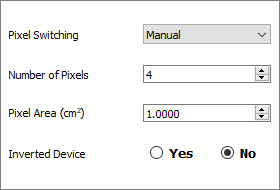
(I) Pixel Switching
Select whether changing the connected pixel is done manually, automatically by the system, or whether to use the external connection on the automated system.
(II) Pixels to Test (Automated Switching)
Select which pixels to measure. The pixel numbers are labelled on the device holder.
(III) Number of Pixels (Automated - External and Manual Switching)
Set the number of individual solar cell pixels in the device being measured.
(IV) Pixel Area
Set the area in cm2 of each pixel in the device.
(V) Inverted Device
Set whether the device to be measured is inverted. This option should be on if the anode of your device connects to the ‘cathode’ pins in the device holder.
9.4 Characterisation Settings
9.4.1 Measurement Settings
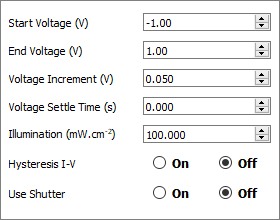
(I) Start Voltage
Set the voltage in volts at which to start the current-voltage measurement. This can be set between -10 V and +10 V.
(II) End Voltage
Set the voltage in volts at which to end the current-voltage measurement. This can be set between -10 V and +10 V.
(III) Voltage Increment
Set the step size in volts for changing the voltage during current-voltage measurement.
(IV) Voltage Settle Time
Set the time in seconds between applying a voltage and measuring the current. This has a maximum of 10 seconds.
(V) Illumination
Set the illumination intensity (in mW.cm-2) being used during the measurement.
(VI) Hysteresis I-V
This option performs a reverse current-voltage measurement after the forward current-voltage measurement has completed.
This reverses the set start and end voltages and uses the same voltage increment and settle time as the forward measurement.
(VII) Use Shutter
If set to On, the Shutter connection on the Source Measure Unit and automated system will be activated during a measurement and deactivated afterwards.
When activated, the shutter outputs a constant 5 V signal.
9.5 Lifetime Settings
9.5.1 Measurement Settings
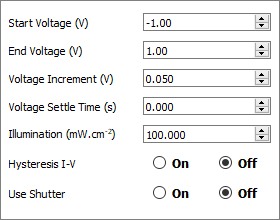
(I) Start Voltage
Set the voltage in volts at which to start the current-voltage measurement. This can be set between -10 V and +10 V.
(II) End Voltage
Set the voltage in volts at which to end the current-voltage measurement. This can be set between -10 V and +10 V.
(III) Voltage Increment
Set the step size in volts for changing the voltage during current-voltage measurement.
(IV) Voltage Settle Time
Set the time in seconds between applying a voltage and measuring the current. This has a maximum of 10 seconds.
(V) Illumination
Set the illumination intensity (in mW.cm-2) being used during the measurement.
(VI) Hysteresis I-V
This option performs a reverse current-voltage measurement after the forward current-voltage measurement has completed.
This reverses the set start and end voltages and uses the same voltage increment and settle time as the forward measurement.
(VII) Use Shutter
If set to On, the Shutter connection on the Source Measure Unit and automated system will be activated during a measurement and deactivated afterwards.
When activated, the shutter outputs a constant 5 V signal.
9.5.2 Lifetime Parameters
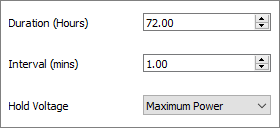
(I) Duration
Set the total duration in hours of the lifetime measurement.
(II) Interval
Set the time interval in minutes between performing repeat current-voltage measurements of the device.
(III) Hold Voltage
Set the voltage that all pixels will be held at between measurements. This can be set as:
- Short-Circuit – hold at 0 V.
- Maximum Power – hold at the average maximum power point determined from most recent current-voltage curve.
- Open-Circuit – hold at the average open-circuit voltage determined from the most recent current-voltage curve.
9.6 Stabilised Current Settings
9.6.1 Measurement Settings
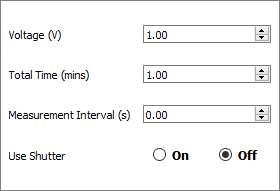
(I) Voltage
Set the voltage to apply to the sample for the measurement. This can be set between -10 V and +10 V.
(II) Total Time
Set the total length of the measurement in minutes.
(III) Measurement Interval
Set the time between each current measurement in seconds.
(VII) Use Shutter
If set to On, the Shutter connection on the Source Measure Unit and automated system will be activated during a measurement and deactivated afterwards.
When activated, the shutter outputs a constant 5 V signal.
9.7 Saving and Loading Settings
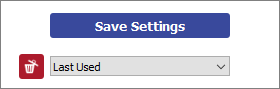
(I) Save Settings
Saves the current settings as a profile that can be loaded quickly for use at another time. When clicked, you will be prompted to name the settings profile.
- If the name is already in use, you will be asked if you wish to overwrite the previous profile.
- The name cannot contain the characters: \ / : * ? “ < > |
The settings profile will be added to the drop-down box using the given name.
(II) Settings Profiles
Select a saved settings profile from the drop-down box. The settings fields will be populated with the saved values.
Settings profiles can be deleted by selecting the profile, and then clicking the red ‘delete’ button next to the drop-down box.
9.8 Saving Results
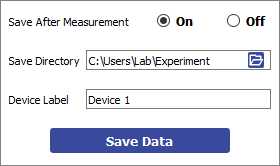
(I) Save After Measurement
Set whether the measurement data will be saved after the measurement has completed.
The program allows for data to be saved automatically and manually once the measurement is complete. For automatic saving, the ‘Saving’ fields must be filled in before the measurement can start, these are detailed below.
For all measurements, a save directory must be specified. This can be done either by:
- Manually typing the directory into the ‘Save Directory’ field.
- Copy and pasting from your file explorer.
- Clicking the file icon button, which will open a dialog box to allow the selection of a folder to save to.
All output files are comma separated variable (.csv) files.
(II) Save Directory
Set the directory in which to create the data files. This can be filled in by:
- Manually typing the directory into the ‘Save Directory’ field.
- Copy and pasting from your file explorer.
- Clicking the ‘Select Directory’ button, which will open a dialog box to allow the selection of a folder to save to.
(III) Device Label
Set the name of the device being tested. This is used to label the files for I-V data and measurement settings.
The field cannot contain the following characters: \ / : * ? “ < > |
(IV) Save Data Format
All data is saved as .csv (comma separated value) files. The figures below show the files that are created when saving data for each of the measurements
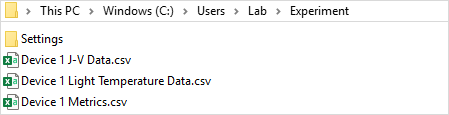
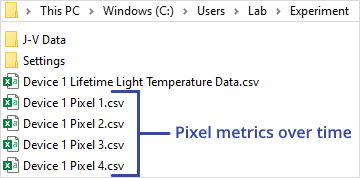
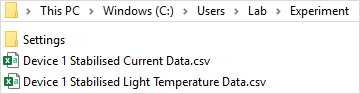
9.9 Controls
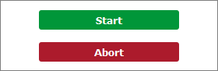
(I) Measure
Clicking this button will start the measurement using the chosen settings. This button cannot be clicked if the software has not detected the test system.
(II) Abort
Stops a measurement that is currently in progress.
9.10 Plot Controls
(I) Position Readout
Whilst the mouse cursor is over the plot in the Characterisation and Stabilised Current tabs, the x and y position of its location are displayed in the bottom-right of the plot, as shown in Figure 9.16.
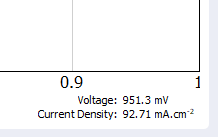
(II) Plot Display Controls
By default, the axes of the plot will automatically scale to display all the data within it. The view can be controlled manually using the following mouse controls:
- Left/Middle click and drag – pan the axes.
- Right click and drag – scale the axes (left-right for x-axis, up-down for y-axis).
- Scroll wheel – scale the axes centred on the cursor location.
A specific axis can be controlled by using these controls on the axis labels. The axes can be reset by clicking the ‘A’ button in the bottom-left of the plot, as shown in Figure 9.17.
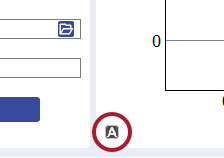
10. Test Devices
The system is shipped with a test device that can be used to check the calibration of the system. They have resistors arranged in the geometry of the substrate pixels, and the appearance of the test device will depend on the substrate system being used (Figure 10.1).
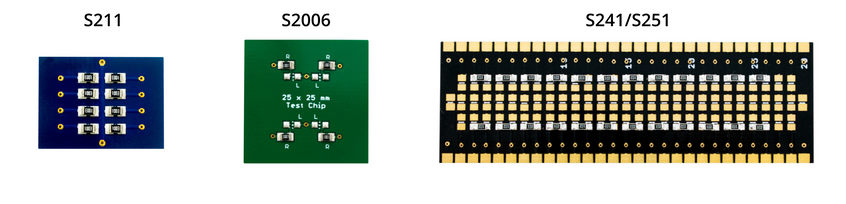
10.1 Taking a Measurement
- Plug in and switch on the system.
- Allow at least 30 minutes for the system to warm up.
- Place the test device in the device holder with the resistors facing up for S211 and S2006 and facing down for S241/S251.
- Start the Solar Cell I-V software and enter the following settings in Figure 10.2.
- These settings can be used with any current range except for the 20 μA range. For this range the start and end voltages must be lowered to -2 V and 2 V respectively.
- The ‘Pixels to Measure’ checkboxes (Automated systems) or ‘Number of Pixels’ (Manual systems) should match the device configuration you have.
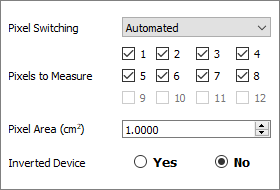
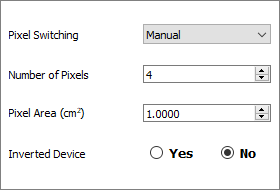
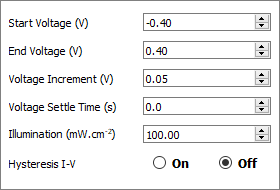
- Click the ‘Measure’ button.
- The system should measure straight line resistor responses from -100 μA.cm-2 to 100 μA.cm-2 (or -20 μA.cm-2 to 20 μA.cm-2 for the 20 μA current range) as shown in Figure 10.3.
- To check the calibration of the system, use the I-V data to calculate the measured resistance at -10 and 10 V (-2 and 2 V for the 20 μA current range).
- Resistance can be calculated using: R = V / I
- For the 200 mA current range the calculated resistance should be between 98 and 102 kΩ (within 2% of the resistor value).
- For all other ranges the calculated resistance should be between 99 and 101 kΩ (within 1% of the resistor value).
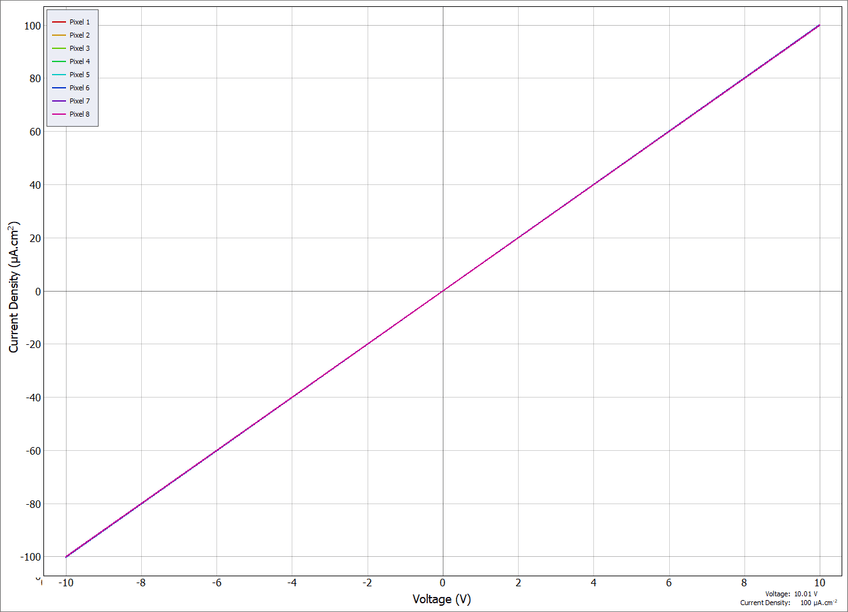
11. Troubleshooting
Most of the issues that may arise will be detailed here. However, if you encounter any issues that aren’t in this list, please contact Ossila.
11.1 Installation and Setup
Problem | Possible Cause | Action |
---|---|---|
No power | The power supply may not be connected properly. | Ensure the system is firmly plugged into the power supply, and that the plug is connected to both the adaptor and a working power socket. |
The power supply adaptor has a fault. | Contact Ossila for a replacement power supply adaptor. | |
Software does not start | The wrong version of Windows is installed on the computer. | Install the software on a computer with Windows Vista or newer. |
The software has not installed properly. | Try reinstalling the software. | |
Cannot connect to the system via USB | The USB cable may not be connected properly. | Ensure the USB cable is firmly plugged in at both ends. |
The USB cable may not be connected to a working USB port. | Try connecting the unit to a different USB port on the computer. | |
The USB cable is defective. | Try using a different USB-B cable, and contact Ossila if necessary. | |
Cannot connect to the system via network | The MAC address of the unit is not registered with the internal network. | Register the system on the network using the MAC address obtained via a USB connection (see Source Measure Unit manual). |
The Ethernet cable may not be connected properly. | Ensure the Ethernet cable is firmly plugged in at both ends. | |
The Ethernet cable is defective. | Try using a different Ethernet cable. |
11.2 Error Messages and Warnings
Message | Description |
---|---|
Current compliance reached | The measured current is greater than the set current limit. |
Error communicating with system | The software is unable to connect to the system. |
No device holder detected | The device holder is not connected to the system properly. |
Voltage increment cannot be zero | The voltage increment is set to 0 V. |
Start and end voltage cannot be equal | The start and end voltages of are set to the same voltage. |
No save directory or device label entered | The save directory and/or the device label fields are empty. |
Settings profile not found | The given settings profile does not exist or is open in other software. |
Error loading settings | There is a problem with the settings profile preventing it from being loaded. |
Error deleting profile | The given settings profile does not exist, the software does not have the necessary permissions to delete it, or it is open in other software. |
No data to save | There is no measurement data in memory to save to file. |
Error saving data | The software does not have the necessary permissions to access the given file path, or the file is already open in other software. |
Error saving settings | The software does not have the necessary permissions to access the given file path, or the file is already open in other software. |
Error creating data directories | The software could not create the directories for save data files. |
Error creating data files | The software could not create the files for saving measurement data. |