Source Measure Unit User Manual
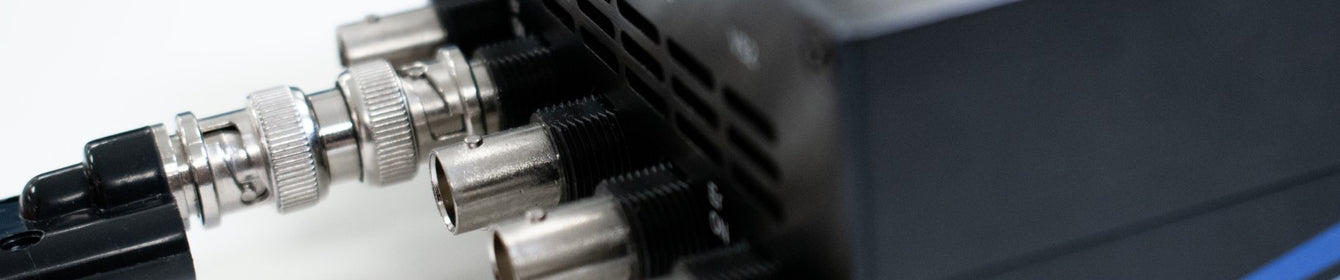
Contents
- EU Declaration of Conformity (DoC)
- Safety
- Requirements
- Unpacking
- Specifications
- Specification Conditions
- Source Measure Units (SMU 1 and SMU 2)
- Voltmeter (Vsense 1 and Vsense 2)
- Measurement Non-Linearity
- Shutter/Trigger
- Physical Specifications
- System Components
- Installation
- SMU Front Panel Software
- Advanced Measurements
- Troubleshooting
- Related Products
Source Measure Unit
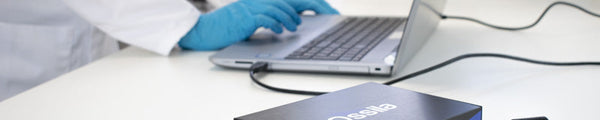
1. EU Declaration of Conformity (DoC)
We
Company Name: Ossila BV
Postal Address: Biopartner 3 Building, Galileiweg 8
Postcode: 2333 BD Leiden
Country: The Netherlands
Telephone Number: +31 (0)718 081020
Email Address: info@ossila.com
declare that the DoC is issued under our sole responsibility and belongs to the following product:
Product: Source Measure Unit – X200 (P2005A2)
Serial Number: P2005A2 - xxxx
Object of Declaration
Source Measure Unit – X200 (P2005A2)
The object of declaration described above is in conformity with the relevant Union harmonisation legislation:
EMC Directive 2014/30/EU
RoHS Directive 2011/65/EU
Signed:
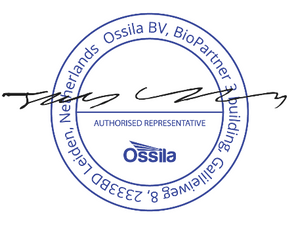
Name: Dr James Kingsley
Place: Leiden
Date: 16/11/2021
Декларация | за съответствие на ЕС |
---|---|
Производител | Ossila BV, Biopartner 3 building, Galileiweg 8, 2333 BD Leiden, NL. |
Декларира с цялата си отговорност, че посоченото оборудване съответства на приложимото законодателство на ЕС за хармонизиране, посочено на предходната(-ите) страница(-и) на настоящия документ. |
[Čeština] | Prohlášení o shodě EU |
---|---|
Výrobce | Ossila BV, Biopartner 3 building, Galileiweg 8, 2333 BD Leiden, NL. |
Prohlašujeme na vlastní odpovědnost, že uvedené zařízeni je v souladu s příslušnými harmonizačními předpisy EU uvedenými na předchozích stranách tohoto dokumentu. |
[Dansk] | EU-overensstemme lseserklærin g |
---|---|
Producent | Ossila BV, Biopartner 3 building, Galileiweg 8, 2333 BD Leiden, NL. |
Erklærer herved, at vi alene er ansvarlige for, at det nævnte udstyr er i overensstemmelse med den relevante EUharmoniseringslovgivning, der er anført på den/de foregående side(r) i dette dokument. |
[Deutsch] | EU-Konformitätserklärung |
---|---|
Hersteller | Ossila BV, Biopartner 3 building, Galileiweg 8, 2333 BD Leiden, NL. |
Wir erklären in alleiniger Verantwortung, dass das aufgeführte Gerät konform mit der relevanten EUHarmonisierungsgesetzgebung auf den vorangegangenen Seiten dieses Dokuments ist. |
[Eesti keel] | ELi vastavusavaldus |
---|---|
Tootja | Ossila BV, Biopartner 3 building, Galileiweg 8, 2333 BD Leiden, NL. |
Kinnitame oma ainuvastutusel, et loetletud seadmed on kooskõlas antud dokumendi eelmisel lehelküljel / eelmistel lehekülgedel ära toodud asjaomaste ELi ühtlustamise õigusaktidega. |
[Ελληνικά] | Δήλωση πιστότητας ΕΕ |
---|---|
Κατασκευαστής | Ossila BV, Biopartner 3 building, Galileiweg 8, 2333 BD Leiden, NL. |
Δηλώνουμε υπεύθυνα όn ο αναφερόμενος εξοπλισμός συμμορφώνεται με τη σχεnκή νομοθεσία εναρμόνισης της ΕΕ που υπάρχει σnς προηγούμενες σελίδες του παρόντος εγγράφου. |
[Español] | Declaración de conformidad UE |
---|---|
Fabricante | Ossila BV, Biopartner 3 building, Galileiweg 8, 2333 BD Leiden, NL. |
Declaramos bajo nuestra única responsabilidad que el siguiente producto se ajusta a la pertinente legislación de armonización de la UE enumerada en las páginas anteriores de este documento. |
[Français] | Déclaration de conformité UE |
---|---|
Fabricant | Ossila BV, Biopartner 3 building, Galileiweg 8, 2333 BD Leiden, NL. |
Déclarons sous notre seule responsabilité que le matériel mentionné est conforme à la législation en vigueur de l'UE présentée sur la/les page(s) précédente(s) de ce document. |
[Hrvatski] | E.U izjava o sukladnosti |
---|---|
Proizvođač | Ossila BV, Biopartner 3 building, Galileiweg 8, 2333 BD Leiden, NL. |
Izjavljujemo na vlastitu odgovornost da je navedena oprema sukladna s mjerodavnim zakonodavstvom EU-a o usklađivanju koje je navedeno na prethodnoj(nim) stranici(ama) ovoga dokumenta. |
[Italiano] | Dichiarazione di conformità UE |
---|---|
Produttore | Ossila BV, Biopartner 3 building, Galileiweg 8, 2333 BD Leiden, NL. |
Si dichiara sotto la propria personale responsabilità che l'apparecchiatura in elenco è conforme alla normativa di armonizzazione UE rilevante indicata nelle pagine precedenti del presente documento. |
[Latviešu] | ES atbils tības deklarācija |
---|---|
Ražotājs | Ossila BV, Biopartner 3 building, Galileiweg 8, 2333 BD Leiden, NL. |
Ar pilnu atbilclību paziņojam, ka uzskaitītais aprīkojums atbilst attiecīgajiem ES saskaņošanas tiesību aktiem, kas minēti iepriekšējās šī dokumenta lapās. |
[Lietuvių k.] | ES atitikties deklaracija |
---|---|
Gamintojas | Ossila BV, Biopartner 3 building, Galileiweg 8, 2333 BD Leiden, NL. |
atsakingai pareiškia, kad išvardinta įranga atitinka aktualius ES harmonizavimo teisės aktus, nurodytus ankstesniuose šio dokumento |
[Magyar] | EU-s megfelelőségi nyilatkozat |
---|---|
Gyártó | Ossila BV, Biopartner 3 building, Galileiweg 8, 2333 BD Leiden, NL. |
Kizárólagos felelösségünk mellett kijelentjük, hogy a felsorolt eszköz megfelel az ezen dokumentum előző oldalán/oldalain található EU-s összehangolt jogszabályok vonatkozó rendelkezéseinek. |
[Nederlands] | EU-Conformiteitsverklaring |
---|---|
Fabrikant | Ossila BV, Biopartner 3 building, Galileiweg 8, 2333 BD Leiden, NL. |
Verklaart onder onze uitsluitende verantwoordelijkheid dat de vermelde apparatuur in overeenstemming is met de relevante harmonisatiewetgeving van de EU op de vorige pagina('s) van dit document. |
[Norsk] | EU-samsvarserklæ ring |
---|---|
Produsent | Ossila BV, Biopartner 3 building, Galileiweg 8, 2333 BD Leiden, NL. |
Erklærer under vårt eneansvar at utstyret oppført er i overholdelse med relevant EU-harmoniseringslavverk som står på de(n) forrige siden(e) i dette dokumentet. |
[Polski] | Deklaracja zgodności Unii Europejskiej |
---|---|
Producent | Ossila BV, Biopartner 3 building, Galileiweg 8, 2333 BD Leiden, NL. |
Oświadczamy na własną odpowiedzialność, że podane urządzenie jest zgodne ze stosownymi przepisami harmonizacyjnymi Unii Europejskiej, które przedstawiono na poprzednich stronach niniejszego dokumentu. |
[Por tuguês] | Declaração de Conformidade UE |
---|---|
Fabricante | Ossila BV, Biopartner 3 building, Galileiweg 8, 2333 BD Leiden, NL. |
Declara sob sua exclusiva responsabilidade que o equipamento indicado está em conformidade com a legislação de harmonização relevante da UE mencionada na(s) página(s) anterior(es) deste documento. |
[Română] | Declaraţie de conformitate UE |
---|---|
Producător | Ossila BV, Biopartner 3 building, Galileiweg 8, 2333 BD Leiden, NL. |
Declară pe proprie răspundere că echipamentul prezentat este în conformitate cu prevederile legislaţiei UE de armonizare aplicabile prezentate la pagina/paginile anterioare a/ale acestui document. |
[Slovensky] | Vyhlásenie o zhode pre EÚ |
---|---|
Výrobca | Ossila BV, Biopartner 3 building, Galileiweg 8, 2333 BD Leiden, NL. |
Na vlastnú zodpovednosť prehlasuje, že uvedené zariadenie je v súlade s príslušnými právnymi predpismi EÚ o harmonizácii uvedenými na predchádzajúcich stranách tohto dokumentu. |
[Slovenščina] | Izjava EU o skladnosti |
---|---|
Proizvajalec | Ossila BV, Biopartner 3 building, Galileiweg 8, 2333 BD Leiden, NL. |
s polno odgovornostjo izjavlja, da je navedena oprema skladna z veljavno uskladitveno zakonodajo EU, navedeno na prejšnji strani/prejšnjih straneh tega dokumenta. |
[Suomi] | EU-vaatimustenm ukaisuusvakuutus |
---|---|
Valmistaja | Ossila BV, Biopartner 3 building, Galileiweg 8, 2333 BD Leiden, NL. |
Vakuutamme täten olevamme yksin vastuussa siitä, että tässä asiakirjassa luetellut laitteet ovat tämän asiakirjan sivuilla edellisillä sivuilla kuvattujen olennaisten yhdenmukaistamista koskevien EU-säädösten vaatimusten mukaisia. |
[Svenska] | EU-försäkran om överensstämmelse |
---|---|
Tillverkare | Ossila BV, Biopartner 3 building, Galileiweg 8, 2333 BD Leiden, NL. |
Vi intygar härmed att den utrustning som förtecknas överensstämmer med relevanta förordningar gällande EUharmonisering som fmns på föregående |
2. Safety
2.1 Warning
- Do NOT connect external voltage sources to either SMU channel.
- The absolute maximum input voltage for the Vsense channels is ±12 V. Do NOT apply input while not powered.
2.2 Use of Equipment
The Ossila Source Measure Unit is designed to be used as instructed. It is intended for use under the following conditions:
- Indoors in a laboratory environment (pollution degree 2).
- Altitudes up to 2000 m.
- Temperatures of 5°C to 40°C; maximum relative humidity of 80% up to 31°C.
The unit is supplied with a 24 VDC power adapter with a power cord for the country of purchase, in accordance with European Commission regulations and British Standards. Use of any other electrical power cables, adaptors, or transformers is not recommended.
2.3 Hazard Icons
The symbols shown in Table 2.1 can be found at points throughout the manual. Note each warning before attempting any associated operations.
Table 2.1 Hazard warning labels used in this manual.
Symbol | Associated Hazard |
---|---|
![]() |
Electrical shock |
2.4 Power Cord Safety

Emergency power disconnect options: use the power cord as a disconnecting method and remove from wall. To facilitate disconnect, make sure the power outlet for this cord is readily accessible to the operator.
2.5 Servicing
If servicing is required, please return the unit to Ossila Ltd. The warranty will be invalidated if:
- Modification or service has taken place by anyone other than an Ossila engineer.
- The unit has been subjected to chemical damage through improper use.
- The unit has been operated outside the usage parameters stated in the user documentation associated with the unit.
- The unit has been rendered inoperable through accident, misuse, contamination, improper maintenance, modification, or other external causes.
2.6 Health and Safety - Servicing

Servicing should only be performed by an Ossila engineer. Any modification or alteration may damage the equipment, cause injury, or death. It will also void your equipment’s warranty.
3. Requirements
The Ossila SMU is compatible with our Front Panel software which is included with the system. It allows for simple operation of the SMU and precision voltmeter channels. Table 3.1 details the minimum computer specifications for the Ossila SMU Front Panel software.
Table 3.1 Ossila SMU Front Panel requirements
Operating Systems | Windows 10 or 11 (64-bit) |
---|---|
CPU | Dual Core 2 GHz |
RAM | 4 GB |
Available Drive Space | 200 MB |
Connectivity |
USB 2.0 Ethernet |
4. Unpacking
4.1 Packing List
The standard items included with the Ossila Source Measure Unit are:
- The Ossila Source Measure Unit.
- 24 VDC power adapter.
- USB-B cable.
- USB memory stick pre-loaded with the user manual, software installer, QC data, and USB drivers.
4.2 Damage Inspection
Examine the components for evidence of shipping damage. If damage has occurred, please contact Ossila directly for further action. The shipping packaging will come with a shock indicator to show if there has been any mishandling of the package during transportation.
5. Specifications
The Ossila Source Measure Unit contains four channels: two source measure units (SMUs) and two precision voltmeters. There is also a general-purpose shutter/trigger to allow other instruments to be controlled or control the unit.
5.1 Specification Conditions
The specifications and information in this document are for the Ossila Source Measure Unit. All units meet these standard specifications when dispatched to the end-user.
The accuracy of both source and measurement of the unit are specified under the following conditions:
- Ambient temperature of 23°C ± 5°C, < 60% relative humidity.
- After a 30-minute warm-up period.
- Default measurement speed (OSR 5) unless specified.
- No filter.
5.2 Source Measure Units (SMU 1 and SMU 2)
The source measure units output a voltage and then measure both the voltage and current. The output voltage is always measured at the output of the BNC (rather than assuming it is at the set voltage) in case of any load effects (for example short circuiting the output or low impedances causing a small drop in voltage). Each source measure unit has manually selectable ranges so that both high and low currents can be measured accurately.
5.2.1 Power Specifcations
The unit is specified for a maximum operation power as in Table 5.1. Figure 5.1 shows the fourquadrant safe operation zone of the unit.
Table 5.1 DC power specifcation
Power per SMU channel (continuous) | |
---|---|
Four-quadrant Operation Source/sink | 2 W (± 10 V at ± 200 mA) |
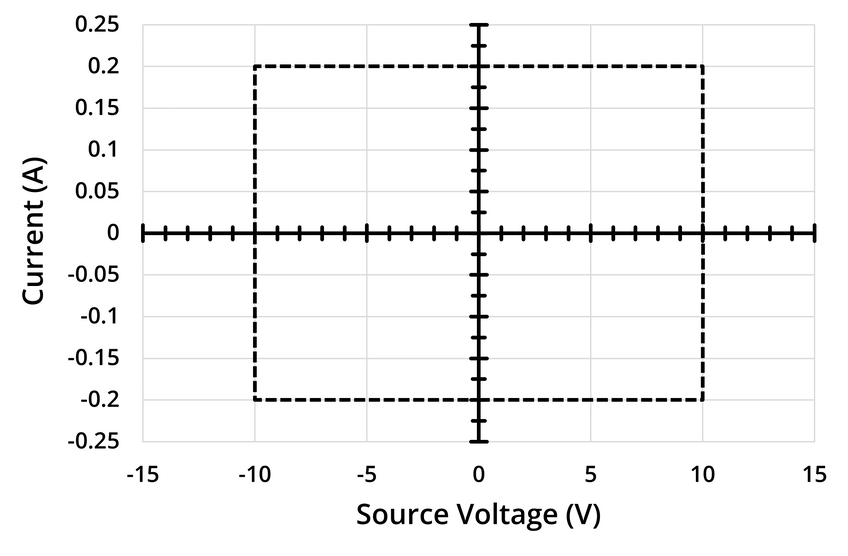
There is some allowance for being beyond these limits (± 10 V and ±200 mA). The unit has internal voltage and current limits set at ±10.5 V and ±225 mA. If a voltage or current greater than these values is measured on either SMU, the red error LED next to the SMU will turn on and the output voltage of the SMU will be set to 0 V. This is a measure to reduce the possibility of damaging the unit due to excessive voltages or currents. The voltage and current limits can be changed programmatically, but they should not be increased past the default values as this will increase the possibility of damaging the unit.
5.2.2 Measurement Speed
The Ossila Source Measure Unit utilises a high-speed, 24-bit no Latency ∆Σ™ ADC. It provides ten speed/ resolution combinations (6.9 Hz/200 nV RMS noise to 3.5 kHz/25 µV RMS noise) which can be selected, with no latency between conversion results. Additionally, a double-speed mode can be selected, enabling output rates up to 7 kHz with one cycle latency. These modes are linked to a single variable called OSR (Oversampling Rate) which is used to program the unit and take the measurement. Table 5.2 lists the various speed settings of the unit, with maximum measurement rates for both SMU and voltmeter channels.
Table 5.2 Measurement speed modes
OSR1 Index | ADC Mode | ADC (samples/data point) | ADC2 RMS Noise | SMU 1/23 (data points/Sec) | Vsense 1/23 (data points/Sec) |
---|---|---|---|---|---|
0 | x1 | 64 | 23 µV | N/A | N/A |
1 | x1 | 128 | 3.5 µV | 525 | 785 |
2 | x1 | 256 | 2 µV | 276 | 414 |
3 | x1 | 512 | 1.4 µV | 142 | 213 |
4 | x1 | 1024 | 1 µV | 72 | 108 |
5 | x1 | 2048 | 750 nV | 36 | 55 |
6 | x1 | 4096 | 510 nV | 18 | 27 |
7 | x1 | 8192 | 375 nV | 9 | 12 |
8 | x1 | 16384 | 250 nV | 4.5 | 6 |
9 | x1 | 32768 | 200 nV | 2.2 | 3 |
1 OSR 10-19 will set the ADC in 2x mode with the same parameters of OSR 0-9, this will approximately double the unit’s measurement rate.
2 ADC noise increases by approximately √2 when OSR is decreased. Note that this is not the unit measurement noise levels.
3 Values based on 1000 data points per measurement.
5.2.3 Voltage Source and Measurement Specifications
Table 5.3 Voltage source and measurement specifications
Mode | OSR | Range | Accuracy | Precision | Resolution |
---|---|---|---|---|---|
Sourcing | N/A | ± 10 V | ± 10 mV | 333 µV | 1.7E-4 |
Measuring | 1 to 4 | ± 10 V | ± 10 mV | 100 µV | 1.0E-4 |
5 to 9 | ± 10 V | ± 10 mV | 50 µV | 1.0E-5 |
5.2.4 Current Measurement Specifiations
The current measurement of the Ossila Source Measure Unit is spread over 5 ranges. Each range has a different maximum current, accuracy, and resolution. As the range number increases, the maximum measurable current decreases, but the accuracy and resolution increase.
Table 5.4 Current measurement specifications
Range | Max Current | Accuracy1 | Precision2 | Resolution | Burden |
---|---|---|---|---|---|
1 | ±200 mA | ±500 µA | 10 µA | 1 µA | < 10mV |
2 | ±20 mA | ±10 µA | 1 µA | 100 nA | < 10mV |
3 | ±2 mA | ±1 µA | 100 nA | 10 nA | < 10mV |
4 | ±200 µA | ±100 nA | 10 nA | 1 nA | < 10mV |
5 | ±20 µA | ±10 nA | 1 nA | 100 pA | < 10mV |
1Accuracy has been measured at the maximum current of that range.
2Precision has been measured at the highest OSR (9).
5.3 Voltmeter (Vsense 1 and Vsense 2)
The Ossila Source Measure Unit has two additional voltage measurement channels marked as Vsense 1 and Vsense 2. They are designed to accurately detect small voltages while simultaneously having a wide dynamic range of ±10 V. Table 5.5 lists the specifications of these additional channels.
Table 5.5 Voltmeter specifcations
OSR | Range | Accuracy | Precision | Resolution |
---|---|---|---|---|
1 to 4 | 1 to 5 | ±10 mV | 100 µV | 1.0E-4 |
5 to 9 | 1 to 5 | ±10 mV | 50 µV | 1.0E-5 |
5.4 Measurement Non-Linearity
The non-linearity in the measurement of the Ossila Source Measure Unit is kept well below the measurement accuracy of every range. Such non-linearity is common due to different amplification stages and analogue digital conversion processes.
5.5 Shutter/Trigger
The Shutter/Trigger can be used either as an input or an output. It can be used to send a trigger signal to other instruments or configured to wait for a trigger from other instruments. The voltage level of the Shutter/Trigger is 5 volts and can source and sink up to 30 mA of current; higher currents may result in damage to the unit.
5.6 Physical Specifications
Table 5.6 Ossila Source Measure Unit physical specifications
Channels |
2 x source measure units (SMUs) 2 x voltmeters (Vsense) 1 x shutter/trigger |
---|---|
Channel Connectivity | BNC |
PC Connectivity |
USB Ethernet |
Dimensions |
Width: 125 mm Height: 55 mm Depth: 185 mm |
Weight | 0.55 kg |
Power Supply | 24 VDC |
6. System Components
The Ossila Source Measure Unit is comprised of the Ossila Source Measure Unit (Figure 6.1) and the Ossila SMU Front Panel Software (Figure 6.2).
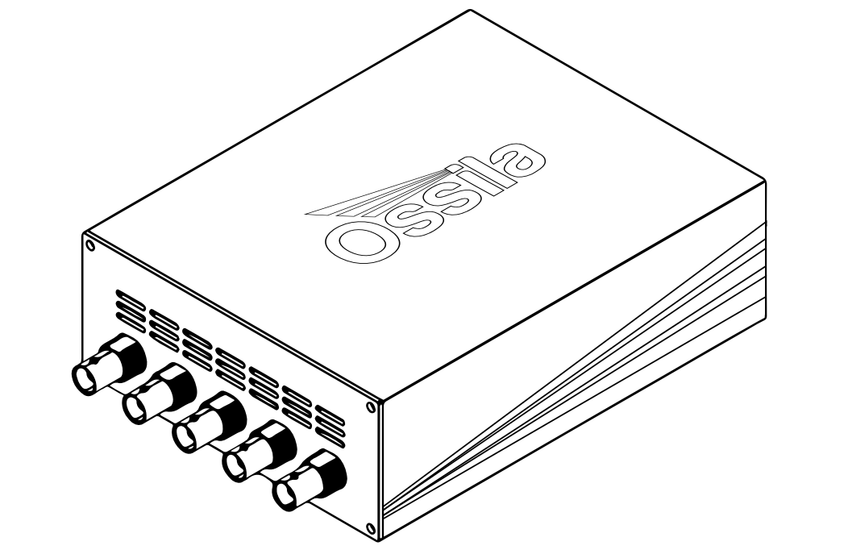
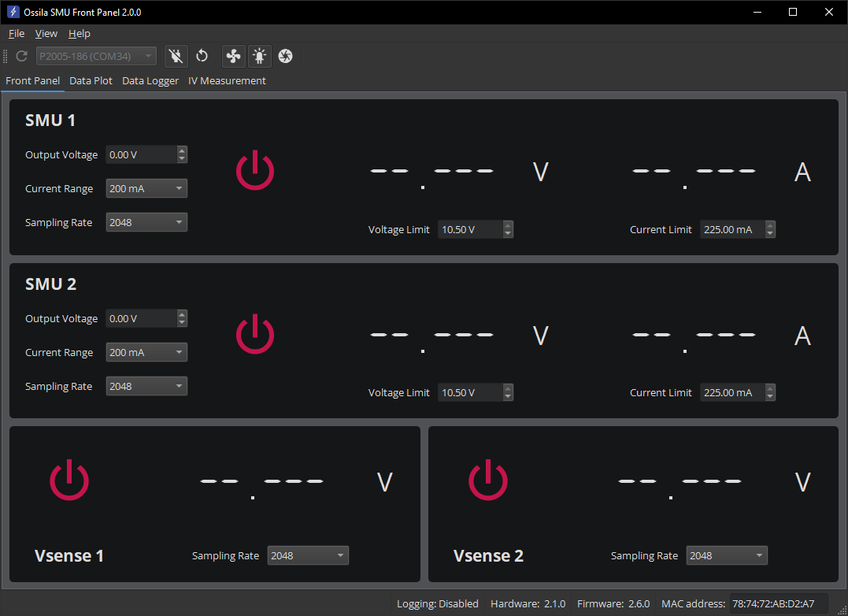
7. Installation
7.1 Power On
- Connect the power supply first to the mains outlet, and secondly to the unit. The red and green power LED (at the back of the unit) and the fan will both switch on.
- Leave for 30 minutes to warm up before performing any measurements.
7.2 USB Driver Installation
- Connect the unit to the computer using a USB cable.
- The USB drivers will be installed automatically. The unit will appear in the Device Manager under the Ports (COM & LPT) section as ‘USB Serial Device (COMX)’ as shown in Figure 7.1.
- Alternatively, the USB drivers can be installed by running the 32-bit or 64-bit installation file located on the USB memory stick provided with the unit.
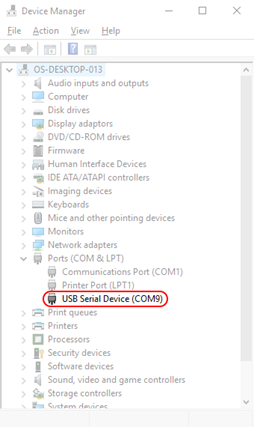
7.3 Connecting to a Network
The Ossila Source Measure Unit is designed to work with any network that supports DHCP. When the ethernet cable is plugged in, the unit will automatically detect and identify the network and register itself within a few seconds
For most networks, the unit will need no further work – simply plug in and wait for the DHCP to work, and it is ready to go. However, there are two situations where more steps are required:
7.3.1 Networks Requiring Device Registration
Some large corporate networks (such as universities) have increased security levels and will only allow “known/registered” devices onto the network. If this is the case for your network, you will need to register the MAC address first. After this, the unit should be allowed on the network and will work as normal via DHCP (fully automatically from this point with no intervention). Many institutions have their own registration systems for computers and printers, and usually have online instructions on how to register a device. If needed, the MAC address of the unit can be obtained by connecting to it with the Front Panel software over USB.
7.3.2 Static IP Networks
For a network without DHCP support, a static IP address must be set manually. This can be done by following these steps:
- Connect the Source Measure Unit to a PC using a USB cable.
- Disable the DHCP client of the device using the command “eth0 set dhcp false”.
- Set the IP address and other network parameters using the command “eth0 set network ip-address subnet-mask gateway-ip dns-ip”
- Save the changes to the board so that they are loaded when the device powers on using the command “eth0 save network”
- Disconnect the USB cable, then connect the Ethernet cable and the device should connect after a few seconds.
Alternatively, an external network router that supports DHCP can be used to connect to a static IP network.
7.4 SMU Front Panel Software Installation
- Run the file ‘Ossila-SMU-Front-Panel-Installer-vX-X-X.exe’ on the USB memory stick provided.
- Follow the on-screen instructions to install the software.
8. SMU Front Panel Software
- Start the Ossila Front Panel software and the window shown in Figure 6.2 will open.
- There are 6 main areas of the UI, which are detailed below:
- Toll Bar
- Front Panel
- Data Plot
- Data Logging
- IV Measurement
- Menu Bar
8.1 Tool Bar

![]() |
Search the USB ports and network for Source Measure Units. Discovered units will be displayed in the drop-down box. |
---|---|
![]() |
Connect to the selected Source Measure Unit. |
![]() |
Disconnect from the selected Source Measure Unit. |
![]() |
Restart the connected Source Measure Unit and reconnect to it. |
![]() |
Toggles the colling fan of the connected Source Measure Unit on and off. |
![]() |
Toggles whether the status LEDs of the SMU channels turn on when the channels are enabled. |
![]() |
Toggles the shutter output on and off. When switched on the shutter outputs 5 VDC. |
8.3 Front Panel
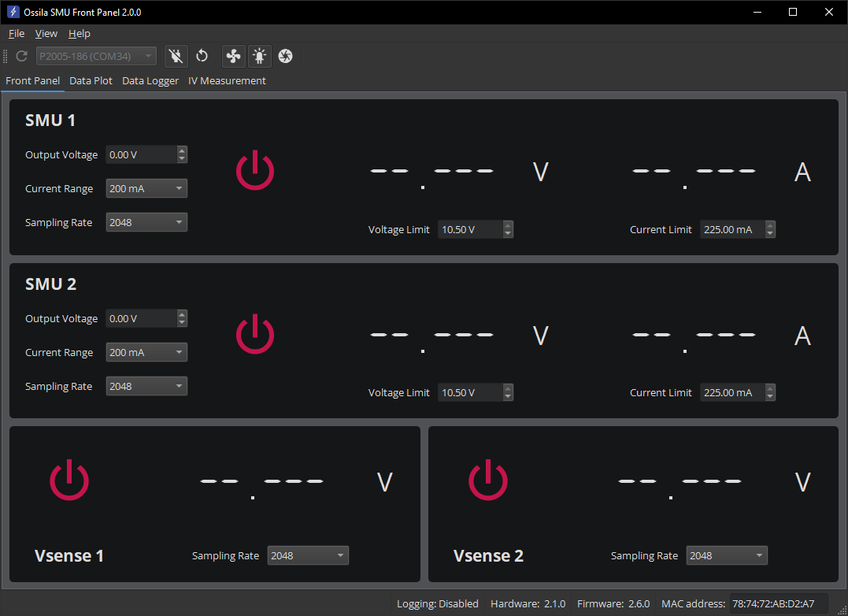
The Front Panel tab consists of a control panel for each of the channels on the Source Measure Unit: SMU 1, SMU 2, Vsense 1, and Vsense 2.

Each SMU panel contains an on/off toggle button, voltage (left) and current (right) measurement displays, and the settings, which are detailed below.
Output Voltage | Sets the output voltage of the SMU channel in volts (maximum of ±10 V). |
---|---|
Current Range | The current range to use for the measurement. This defines the upper limit and sensitivity of current measurements as shown in Table 5.4. |
Sampling Rate | The number of samples to take for each data point (the OSR, see Section 5.2.2 for details). A higher sampling rate will increase the accuracy of a measurement but will increase the time taken for it to be performed. |
Voltage Limit | The maximum voltage that the SMU channel can source. If output voltage is greater than this value, the output voltage will be automatically set to 0 V. |
Current Limit | The maximum current that the SMU can measure. If measured current is greater than this value, the output voltage will be automatically set to 0 V. |
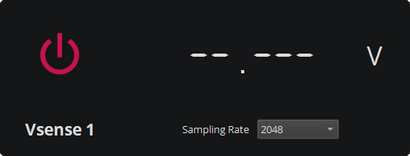
Each Vsense panel contains an on/off toggle button, the voltage measurement display, and the settings, which are detailed below.
Sampling Rate | The number of samples to take for each data point (the OSR, see Section 5.2.2 for details). A higher sampling rate will increase the accuracy of a measurement but will increase the time taken for it to be performed. |
---|
8.4 Data Plots

The Data Plots tab contains a pair of plots that display the last 300 live voltage and current readings from each of the channels on the Source Measure Unit. The upper plot displays voltage readings, and the lower plot displays current readings. Controls for channels and plotting can be found in the sidebar.
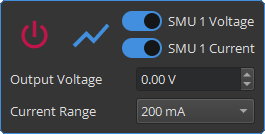
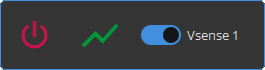
Each SMU panel contains an on/off toggle button, a legend line indicating the line colour for the device data, switches for toggling whether SMU data are displayed in the plots, and controls for Set Voltage and Current Range as described in Section 8.3. Vsense panels contain an on/off toggle, a legend line, and a switch for toggling Vsense data display.
Below the device control panels are the plot control buttons, detailed below.
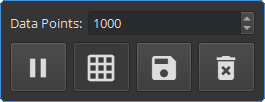
Data Points | The number of data points to plot for each channel. |
---|---|
![]() |
Resume plotting data. |
![]() |
Pause plotting data. |
![]() |
Toggle the gridlines on the plot on and off. |
![]() |
Save the data in the plots to a comma separated value (.csv) or text (.txt) file. A file dialog will open to allow you to select a save file name and location. |
![]() |
Clear all data from the plots. A confirmation dialog box will be displayed. |
8.3.1 Plot Display Controls
By default, the plots will automatically scale the axes of the plot to display all the data within it. The view can be controlled manually using the following mouse controls:
- Left or middle click and drag – pan the axes.
- Right click and drag – scale the axes.
- Scroll wheel – scale the axes.
A specific axis can be controlled by using these controls on the axis labels. The axes can be reset by clicking the ‘A’ button in the bottom-left of the plot, as shown in Figure 8.9 (note, this button will only appear whilst the mouse cursor is over the plots).
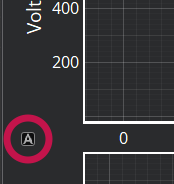
8.5 Data Logging
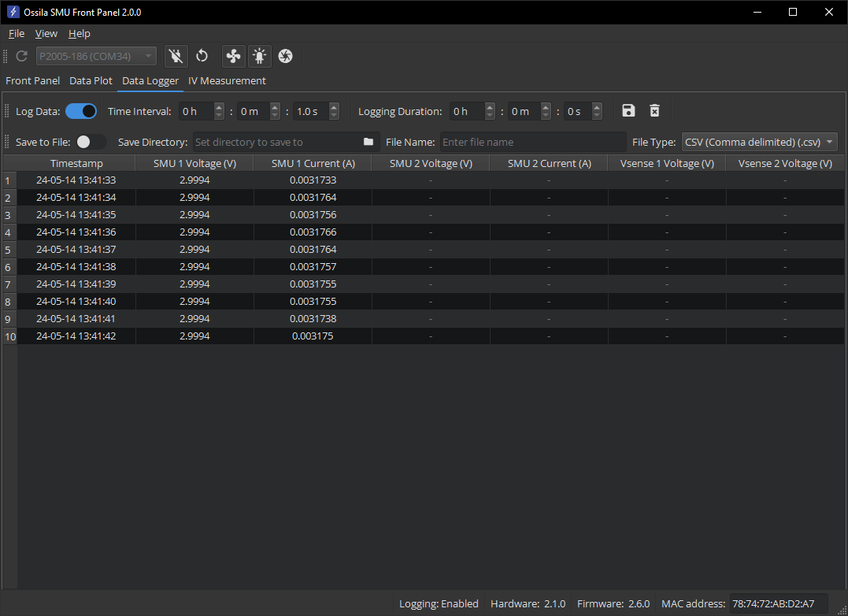
TThe Data Logger tab contains controls for periodically recording measurement data of the SMU and Vsense channels. Logged data is displayed in the data table and can optionally be saved to file as it is logged. There are several controls that can be used to customise data logging:
Log Data | Toggle data logging on and off. |
---|---|
Time Interval | The time to wait between logging measurements. |
Logging Duration | The total duration to log data for. Logging will be automatically disabled when the duration has elapsed. The remaining duration is displayed on the right side of this tool bar. |
![]() |
Save the data in the table to a CSV (comma delimited) (.csv) or text (tab delimited) (.txt) file. A file dialog will open to allow you to select a save file name and location. |
![]() |
Clear all data from the table. A confirmation dialog box will be displayed. |
Save to File | Toggle saving the data to file as it is logged in the table. The Save Directory, File Name, and File Type must be set to enable saving. |
Save Directory | The file directory in which the saved data file is located or will be created. Clicking the file icon will open a dialog to browse to a directory. |
File Name | The name of the file to save data to. If the file does not exist, it will be created before logging any data. |
File Type | The type of file to save data to, CSV (comma delimited) (.csv) or text (tab delimited) (.txt). |
8.4.1 Copying Data
Select the table cell or cells of the data to be copied, then either:
- Right-click on the highlighted cells and select ‘Copy’ from the menu.
- Press the copy keyboard shortcut (CTRL + C on Windows).
8.4.2 Deleting Table Rows
Select at least one row in each row to be deleted, then either:
- Right-click on the highlighted cells and select ‘Delete’ from the menu.
- Press the delete keyboard shortcut (Delete on Windows).
A confirmation dialog will appear before any data is deleted.
8.5 IV Measurement
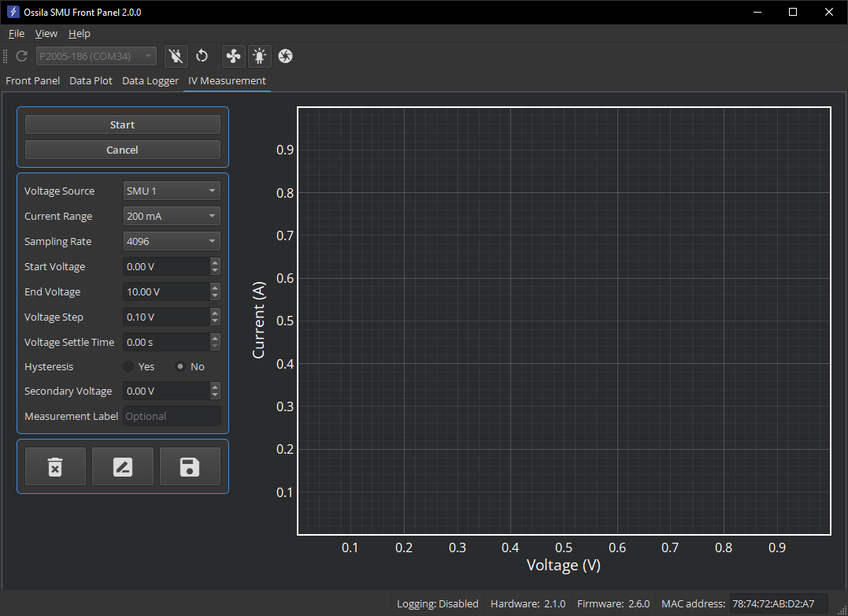
The IV Measurement tab contains controls for perform current-voltage (IV) measurements. The measurement can be customised with the following settings:
Voltage Source | Which SMU channel to use for the IV measurement. |
---|---|
Current Range | The current range to use for the measurement. If autorange is selected, the software will automatically select the most appropriate range during the measurement. |
Sampling Rate | The number of samples to take for each data point (the OSR, see Section 5.2.2 for details). |
Start Voltage | The voltage in volts at which to start the measurement. |
End Voltage | The voltage in volts at which to end the measurement. |
Voltage Step | The step size in volts for changing the voltage during the measurement. |
Voltage Settle Time | The time in seconds between outputting a new voltage and measuring the current. |
Hysteresis | Whether to perform a reverse IV measurement after the forwards measurement has completed. The reverse measurement uses the same settings as the forwards measurement, except with start and end voltages swapped. |
Secondary Voltage | The voltage in volts to be output by the SMU channel not selected as the Voltage Source for the IV measurement. If set to 0 V, this will not be used. |
Measurement Label | An optional label to give the IV measurement. Used to identify the measurement in the legend and selection windows. |
When any of the below buttons are clicked, the window shown in Figure 8.11 will open to allow selection of one or more IV measurements. Note, when relabelling, only a single measurement can be selected.
![]() |
Select IV measurements and save them to a CSV (comma delimited) (.csv) or text (tab delimited) (.txt) file. |
---|---|
![]() |
Select an IV measurement to change the label of. |
![]() |
Select IV measurements to delete. |
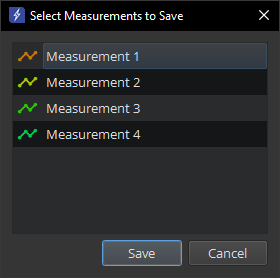
8.5.1 Plot Display Controls
The IV Measurement plot has the same controls as detailed in Section 8.3.
8.6 Menu Bar
8.6.1 File
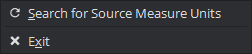
Search for Source Measure Units | Search the USB ports and network for Source Measure Units. Discovered units will be displayed in the drop-down box in tool bar. |
---|---|
Exit | Close the software. |
8.6.2 View
Toggle Theme | Switch the software between light and dark themes. |
---|
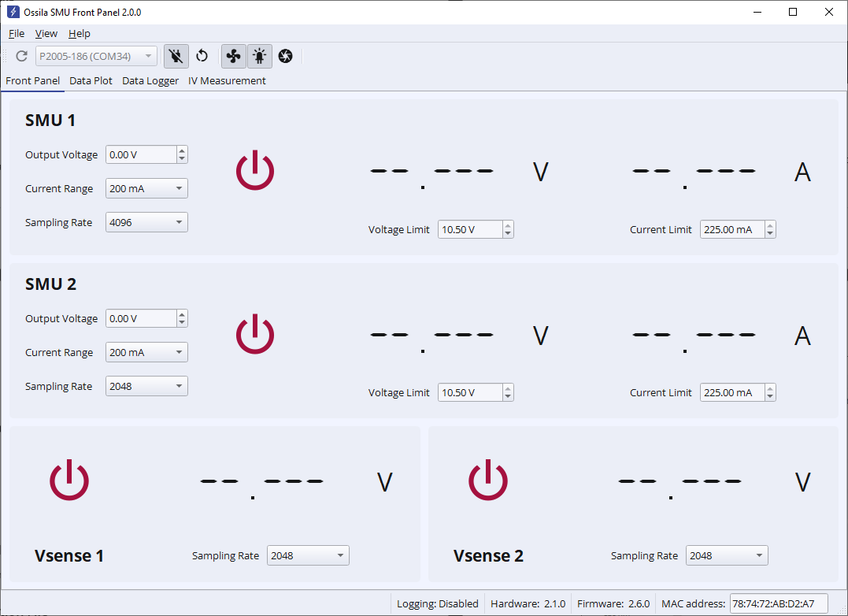
8.6.3 Help
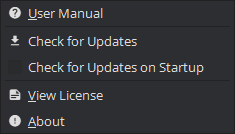
User Manual | Open the user manual in your default web browser. |
---|---|
Check for Updates | Check whether a newer version of the software is available to download and install. If an update is available a message will be displayed in the status bar with the latest version number. Clicking the message will take you to Ossila’s website where you can download the new version. |
Check for Software Updates on Startup | When checked the software will automatically check for software updates each time it starts. |
License | Display software license information. |
About | Display information about the software. |
9. Advanced Measurements
If you want to perform a measurement that is not covered by the Front Panel software, you can control the Source Measure Unit directly using a variety of programming languages. More information and the available commands can be found in the Programming Documentation
10. Troubleshooting
Most of the issues that may arise will be detailed here. However, if you encounter any issues that are not detailed here, then please contact Ossila.
Table 10.1 Troubleshooting guidlines for the Ossila Source Measure Unit.
Problem | Possible Cause | Action |
---|---|---|
No power | The power supply may not be connected properly. | Ensure the system is firmly plugged into the power supply, and that the plug is connected to both the adaptor and a working power socket. |
The power supply adaptor has a fault. | Contact Ossila for a replacement power supply adaptor. | |
Software does not start | The wrong version of Windows is installed on the computer. | Install the software on a computer with Windows 10 or newer. |
The software has not installed properly. | Try reinstalling the software. | |
Cannot connect to the system via USB | The USB cable may not be connected properly. | Ensure the USB cable is firmly plugged in at both ends. |
The USB cable may not be connected to a working USB port. | Try connecting the unit to a different USB port on the computer. | |
The USB cable is defective. | Use a different USB-B cable, and contact Ossila if necessary. | |
The USB drivers may not be installed or may not have installed properly. | Try installing or reinstalling the drivers, they can be downloaded from the address given in the Software Installation section. | |
Cannot connect to the system via network | The MAC address of the unit is not registered with the internal network. | Register the system on the network using the MAC address obtained via a USB connection (Section 7.3: Connecting to a Network). |
The Ethernet cable may not be connected properly. | Ensure the Ethernet cable is firmly plugged in at both ends. | |
The Ethernet cable is defective. | Try using a different Ethernet cable. |