Spin Coater
Lab Equipment, Thin Film CoatingLow Price, Vacuum-Free and Compact Spin Coater
Produce high-quality films anywhere with no vacuum system needed
Overview | Advanced or Standard? | Specifications | Features | Gallery | In the Box | Accessories | Resources and Support
Vacuum-free Ossila spin coaters are ideal for spin coating in busy, fast-paced labs. These systems are robust, affordable, and trusted by academics and researchers around the world.
With a compact design and no vacuum required, this system can easily fit into any laboratory or glove box. The Ossila Spin Coater relies on a multi-substrate chuck that accommodates four popular substrate sizes and is optimized for excellent film quality. You can also design your own unique chuck to fit your substrates.
Both standard and advanced models have programmable controls, allowing you to save multi-step programmes, controlling spin speeds and times with high precision. You can also have your own user profile, with multiple recipes pre-saved, perfect for shared research facilities. For controllable, automated dispensing of solvents, combine our spin coaters with either our single or dual syringe pump with the Ossila Spin Coating System.
Spin Coating System
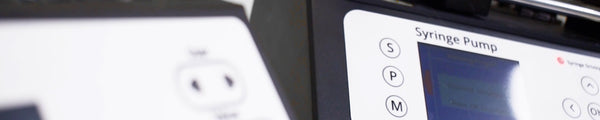
Vacuum-Free
Innovative chuck design
Range of Speeds
Up to 6,000 or 10,000 rpm
Long Spin Cycles
Up to 1,000 or 3,600 seconds
Built to Last
Durable & chemical-resistant
Spin Coater Advanced vs. Standard
Standard Model | Advanced Model | |
---|---|---|
Speed Stability | <2% error | <0.25% error |
Speed | 120 – 6,000 rpm | 500 – 10,000 rpm |
Spin Time | 1 – 1,000 sec | 1 – 3,600 sec |
User Profiles | 10 | 15 |
Materials | Polypropylene bowl, steel casing, tempered glass lid | PTFE bowl, powder coated steel casing, tempered glass lid |
Weight | 2.75 kg | 3.7 kg |
Why Go Vacuum-Free?
There are some issues with vacuum-based spin coating including:
- Substrate warping with thin films affecting coating uniformity.
- Force of vacuum on solutions through porous substrates, such as ceramics, can lead to inhomogeneity across the film.
- Increased maintenance time and costs due to vacuum pump breaking or solvent damage.
- Expensive and inconvenient to build vacuum-based spin coater into lab benches and glove boxes.
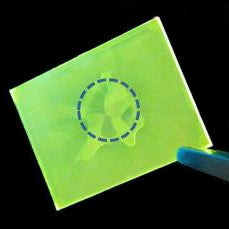
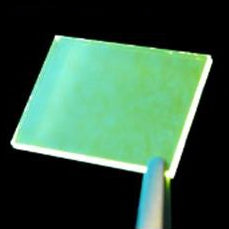
Our vacuum-free chucks ensure an even film distribution by keeping your substrates flat and free from damage, even if they are flexible. Excess coating material is drained away during coating with no warping of thin substrates.
Without a vacuum line, the Ossila Spin Coater can be set up anywhere with a single mains socket—spin coat on a lab bench, in a fume hood, or a glove box all in the same day.
Specifications
Additional Specifications
Max Substrate Size | 100 mm (4") diameter |
---|---|
Programs | 10 programs, , with up to 50 steps each, on each user profile |
Safety Switch | Magnetic safety switch on the door |
Additional Features | Built-in spirit level and adjustable feet |
Dimensions (D x W x H) | 225 mm x 170 mm x 140 mm (8.86" x 6.69" x 5.51") |
Power Supply | DC 24 V 2 A, via 100–240 V 50/60 Hz power adapter |
Spin Coater Chuck Specifications
L2001U1/L2001U2 Standard Spin Coater Chuck
Choose between polypropylene, PTFE, or PEEK chuck material depending on your application. The design incorporates all of the most commonly used substrates including:
Plus, our chucks also have:
- A rimmed edge to improve air flow uniformity and reduce solvent build up within the bowl.
- Simplified drainage channels to reduce buffeting and improve the stability of the chuck.
- Finger cutouts for easy removal of chucks, allowing you to switch them for different experiments.
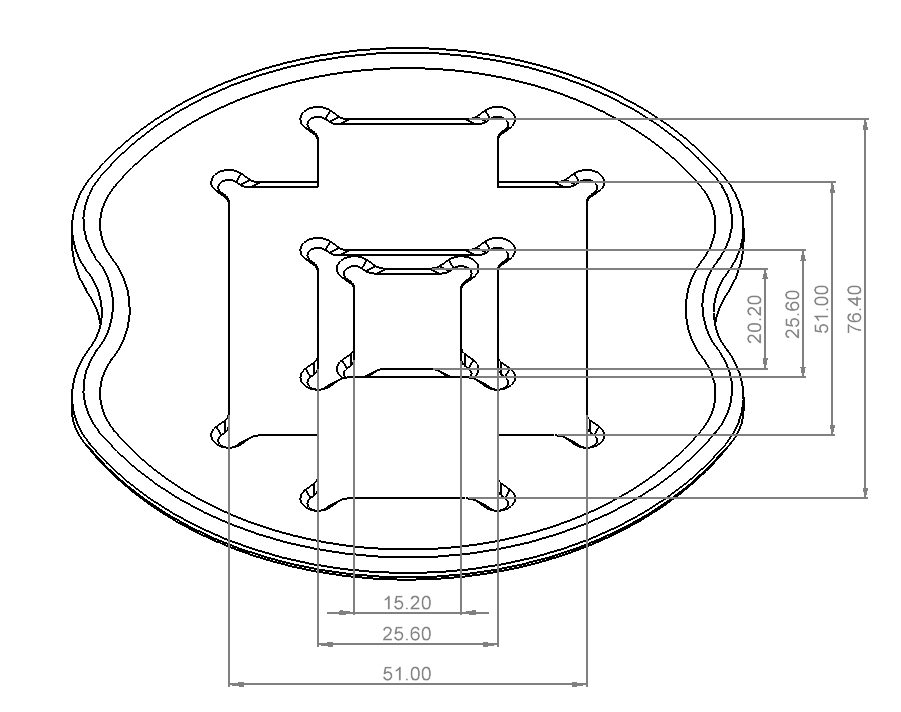
Custom Chucks
Custom chucks are available at a discounted price with the purchase of a spin coater, but can also be purchased separately. Please contact us to discuss your needs, specifying the length, width, and height of each substrate. Alternatively, STL, STEP, and SLDPRT files (for AutoCAD / FreeCAD and SolidWorks respectively) are freely available to download should you wish to create your own chucks.
Custom Chuck Requirements
Maximum Chuck Diameter | 115 mm (4.5") |
---|---|
Maximum Substrate Diameter | 100 mm (4") |
Blank Chuck Downloads
Version 2
Version 1
- .STL file for AutoCAD and TurboCAD
- .SLDPRT file for SolidWorks
Manual
We recently purchased an Ossila Spin Coater. Its compact size and vacuum-free system is ideal for our rather over-crowded laboratory, and it has enabled us to prepare a series of high-quality block copolymer thin films. The chucks make it easy to use different substrates and we have programmed several spin cycles, which allows systematic variation of the copolymer film thickness with good reproducibility.
Professor Steve Armes FRS, Professor of Polymer and Colloid Chemistry, University of Sheffield
Spin Coater Features
Vacuum-Free
Ossila spin coaters can produce uniform films with zero substrate warping or damage, even when coating flexible substrates. Without a vacuum line to connect, simply plug the spin coater and get started on your research.
Large Range of Speeds
In our standard model, spin speeds range from 120 to 6,000 rpm, covering a range of different spin coating conditions—from slow dry crystallization to ultra-thin films. Or choose the advanced model for spin speeds from 500 to 10,000 rpm with an error margin of 0.25% for advanced electronics and optics, or coating with high viscosity materials
Long Spin Cycles
With our advanced model, extend your spin cycles up to 3,600 seconds to achieve better solvent evaporation and more controlled layer formation. Useful for multilayer coatings and graded film properties in the development of advanced materials, and biocompatibility in biotechnology applications.
Multi-Substrate Chuck
The included chuck holds four common substrate sizes without the need to switch between chucks. The opitmized chuck design improves airflow over the substrate, reduces solvent build up, and ensures mechanical stability at very high rotational speeds. Choose from polypropylene, PTFE or PEEK chuck to match your coating solution.
Durable and Chemical-Resistant Materials
Both models are constructed with materials that ensure high chemical resistance, prolonging the lifetime of the system. For enhanced durability, the advanced model comes equipped with a PTFE bowl and chuck as standard, with an optional upgrade to a PEEK chuck for even greater resilience.
Full Control
The inbuilt control system allows you to have 10 separate user profiles — with each profile capable of saving 10 recipes with up to 50 steps. Plus, the spirit level and adjustable feet make it simple to achieve a flat spinning axis. Perfect for uniform films in a busy lab.
I use a Contact Angle Goniometer and Spin Coater from Ossila, the best tools I have ever used for the application of Perovskite solar cells. I plan to order more devices from the same brand.
Ashique Kotta, Jeonbuk National University
Spin Coater Gallery
In the Box
- Ossila Spin Coater
- Multi-substrate spin coater chuck
- Power supply
Accessories
Resources and Support
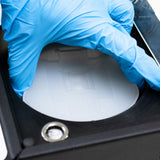
The advanced model offers more control than the classic spin coater in a wide range of areas. These advancements make it ideal for high-precision and demanding applications.
Read more...