FTO Substrates: Adapting Unpatterened Substrates for Photovoltaic Devices

As part of our photovoltaic substrate system, Ossila offers patterned Indium Tin Oxide (ITO) substrates which are designed to work with our evaporation masks to create multi pixel devices. The electrode contacts on the ITO substrate also align with the connection pins in our electronic test boards, which lets us measure devices quickly and easily.
While ITO has been the standard in the field for creating organic electronic devices, it is less suitable for fabrication methods that require annealing at high temperatures, such as perovskites, dye sensitized solar cells, and CZTS.
An alternative transparent electrode material is Fluorine-doped Tin Oxide (FTO). FTO can withstand the high temperatures that ITO cannot, yet it still provides a transparent electrical connection to the pixels in a device.
Ossila provides patterned ITO substrates, however the processes used to pattern the ITO will not work with FTO, and therefore we can currently only provide unpatterned FTO substrates.
In this guide, we will explain how to use the unpatterned FTO glass substrates to create devices with Ossila evaporation masks and test them with our compatible test board.
Patterning FTO Substrates
One of the most common methods for patterning FTO is to chemically remove the FTO from specific areas on the substrate, using a process known as chemical etching. We find that the most effective way to chemically etch is by using etch-resistant tape, zinc powder and hydrochloric acid.
For etching of FTO-coated glass, you will need the following products:
- Tec 8 (S301) / Tec 10 (S302) / Tec 15 FTO (S304) glass
- Etch resistant tape
- Zinc Powder
- Hydrochloric acid
- Cleanroom swabs
- Precision Spatula
The etching procedure is shown schematically in Figure 1, from the top and side perspectives.
- Prepare a 2M solution of hydrochloric acid (HCl).
- Take an unpatterned FTO substrate and apply a 6mm wide piece of etch resistant tape along its centre, perpendicular to the longest edge (Figure 1a). This will protect the area of the FTO that you don’t want to etch away.
- Using a spatula, apply zinc powder evenly across the surface of the substrate (Figure 1b). Remove any excess zinc powder from the surface by shaking the substrate lightly.
- Place the substrate into glassware and cover the surface in hydrochloric acid. This will start a reaction between the hydrochloric acid, the zinc powder and the FTO (Figure 1c).
- Leave the substrate for 3 minutes for the reaction to complete.
- Rinse away any excess hydrochloric acid using deionized water, and firmly wipe away any leftover residue using a cotton bud. You should be left with an FTO strip covered in tape (Figure 1d).
- Peel away the tape and remove any remaining adhesive using isopropyl alcohol. You will be left with a 6mm wide strip of FTO (Figure 1e).
Fabricating FTO Devices
To fabricate devices on top of the FTO strip, we recommend using the Ossila E503 Multi-Electrode/Busbar Mask (Figure 2).
You can use this mask to create eight pixels on top of the FTO strip that you made in the previous section. The device creation process is shown in Figure 3.
- Deposit the appropriate device layers on the FTO strip (Figure 3b).
- Using a scalpel or sharp tweezers, scratch away a section of the device layers at the top and bottom of the FTO strip (Figure 3c). This will expose the FTO and provide a good contact between the FTO and evaporated electrode strips in the final device.
- Place the substrate in the evaporation mask and deposit the electrodes (Figure 3d). The outermost strips will provide electrical contact with the FTO strip, which acts as a common anode.
- The ‘fingers’ on the left and right will overlap the device layers and FTO strip, creating cathodes for each of the pixels (Figure 3e).
Figure 4 shows a larger version of Figure 3e. The scratch in the active layer is filled during the evaporation, providing a pathway for current to travel from the FTO anode to the evaporated electrode (top contact). This completes the circuit of the device. The pixels of the device, the areas where both the FTO and evaporated cathodes overlap the device layers, are highlighted yellow.
Testing FTO Devices
The final device will have 8 cathode connections and two anode connections (top and bottom). These align with the contact pins on the E371 Push-Fit Test Board (Figure 4).
The device is positioned within the test board, and the switches are used to determine the pixel under test. The BNC socket can be connected to a source measure unit (SMU) for cell characterisation.
Ossila also provides a complete Solar Cell I-V Test System, which connects to the Push-fit test board and will perform the characterisation for you. There is also an automated version of the system, which removes the need for manually switching between pixels.
Solar Cell I-V Test System
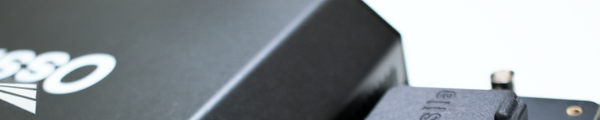
Learn More

Organic solar cells, also known as photovoltaics (OPVs), have become widely recognized for their many promising qualities. This page introduces the topic of OPVs, how they work and their development.
Read more...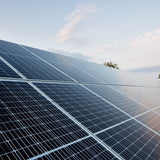
A solar cell is a device that converts light into electricity via the ‘photovoltaic effect’. They are also commonly called ‘photovoltaic cells’ after this phenomenon, and also to differentiate them from solar thermal devices. The photovoltaic effect is a process that occurs in some semiconducting materials, such as silicon.
Read more...