How are Carbon Nanotubes Made?
There are multiple methods for producing carbon nanotubes (CNTs) whether they are multi-walled carbon nanotubes (MWCNT) or another kind. They usually involve gas phase processing. The three key methods are; chemical vapour deposition (CVD), laser ablation and arc discharge. The table below compares the three key methods and various features:
Chemical Vapour Deposition | Laser Ablation | Arc Discharge | |
---|---|---|---|
Yield rate |
High 20–100% |
Moderate 70% max |
Good 30–90% max |
Purity |
High |
High |
High |
Materials |
Range of Hydrocarbons |
Graphite |
Pure graphite |
Accessibility of Materials |
Abundant |
Less accessible |
Less accessible |
Conditions |
High temperatures within 500 - 1000 C at atmospheric pressure |
Argon or nitrogen gas at 500 Torr Post treatment |
Low-pressure inert gas (helium) Post treatment |
Energy Requirement |
Moderate |
High |
High |
Reactor Design |
Easy |
Difficult |
Difficult |
Production Rate |
High |
Low |
Low |
Advantages |
|
|
|
Disadvantages |
|
|
|
Chemical Vapour Deposition (CVD)
One of the key methods for synthesising carbon nanotubes is chemical vapour deposition (CVD). Various forms of CVD exist, including:
- catalytic chemical vapor deposition (CCVD) - thermal or plasma-enhanced (PE)
- oxygen-assisted CVD
- water-assisted CVD
- microwave plasma CVD (MPECVD)
- radiofrequency CVD (RF-CVD)
- hot-filament CVD (HFCVD)
CCVD is the most common of these techniques. The continuous process involves chemically breaking down hydrocarbons so that the carbon atoms can reform bonds in a nanotube shape. The chosen substrate is placed in an oven, heated to a high temperature (~ 700°C) and hydrocarbon gas is fed in slowly. The gas decomposes and when the carbons come into contact with metal catalyst nanotubes form.
In practice, nanotube structures are etched into silicon and embedded with iron nanoparticles at the base. A hydrocarbon, such as acetylene, is then heated and decomposed onto the substrate. When the carbon comes into contact with the metal particles embedded in the etched holes, it starts to form nanotubes, which align with the shape of the tunnel. CVD allows for the growth of highly aligned and long carbon nanotubes in the direction of the tunnel.
Common catalyst particles include nickel, cobalt, iron, or their combinations. Using these metal nanoparticles in conjunction with a catalyst support increases the surface area. This improves the efficiency of the catalytic reaction between pure carbon and the metal particles.
Laser Ablation
Laser ablation is another key technique for producing carbon nanotubes. It has the potential to produce CNTs with high purity and quality. The process involves high-power laser vaporization (YAG type). A quartz tube containing a block of pure graphite and metal (cobalt or nickel) particle catalysts is heated inside a furnace at approximately 1,200°C in an argon atmosphere. The laser vaporizes the graphite and in the presence of the metal catalyst carbon nanotubes form.
The diameter of the nanotubes produced depends on the laser power: as the laser pulse power increases, the nanotube diameter decreases. Ultrafast (subpicosecond) laser pulses have the potential to produce large quantities of carbon nanotubes.
Several parameters influence the properties of CNTs synthesized by the laser ablation method, including:
- Structural and chemical composition of the target material
- Laser properties:
- peak power
- continuous wave vs. pulse
- energy fluence
- oscillation wavelength
- repetition rate
- Buffer gas flow and pressure
- Chamber pressure
- Chemical composition
- Distance between the target and the substrates
- Ambient temperature
The main advantages of this technique is that it produces a relatively high yield with low metallic impurities. This is a result of the metal atoms tendency to evaporate from the ends of the nanotubes once they close. However, a key drawback is that the nanotubes produced by this method are not always uniformly straight and may have some branching.
The laser ablation method is not cost-effective as it requires high-purity graphite rods and significant laser power (sometimes involving two laser beams). The quantity of nanotubes produced per day is lower compared to the arc-discharge technique.
Arc Discharge
Arc discharge is another key technique for accessing carbon nanotubes. It uses high temperatures (> 1,700°C) which causes the expansion of CNTs and results in fewer defects. The most common method uses arc discharge between high-purity graphite electrodes which are usually water-cooled. They are usually within a chamber filled with helium (500 torr) 1 - 2 mm apart at sub atmospheric pressure. Inside the chamber there is a graphite cathode and anode, evaporated carbon molecules and metal catalyst particles such as cobalt, nickel, or iron.
A direct current is passed through the chamber, which is pressurized and heated to approximately 4,000 K. At 100 amps carbon vaporizes and forms hot plasma. During this process, about half of the evaporated carbon solidifies at the tip of the cathode, forming a deposit at a rate of 1 mm/min, known as a ‘cylindrical hard deposit’ or ‘cigar-like structure,’ while the anode is consumed. The remaining carbon forms a hard gray shell on the chamber walls, known as ‘chamber soot,’ and ‘cathode soot’ on the cathode itself. The inner core, cathode soot, and chamber soot yield either single-walled or multi-walled carbon nanotubes, as well as nested polyhedral graphene particles.
For synthesising MWCNTs a catalyst is not always required. However, for SWCNT metal catalysts must always be used. A complex anode comprised of graphite and metal such as:
- gadolinium (Gd)
- cobalt
- nickel
- iron
- silver
- platinum
- palladium
- mixtures: Co-Pt, Co-Ru, Ni-Y, Fe-Ni, etc.
Studies have shown that a Ni-Y-graphite mixture can yield high amounts of SWCNTs (with an average diameter of 1.4 nm). This mixture is now widely used for large-scale SWCNT production.
The main advantage of the arc-discharge technique is its ability to produce large quantities of nanotubes. However, a key disadvantage is the limited control over the nanotube alignment (chirality), which is crucial for their characterization and function. Additionally, since a metallic catalyst is needed for the reaction, the final product requires purification.
Other Methods for Synthesising Carbon Nanotubes
Other methods for producing carbon nanotubes that are less common include:
- gas phase catalytic process (HiPCO)
- flame synthesis
- core shell polymer microsphere method
- aerosol precursor method
- arc water process
- low temperature route
- plasma method
- fluidized bed method
- nebulized spray process
Multi-Walled Carbon Nanotubes (MWCNT)
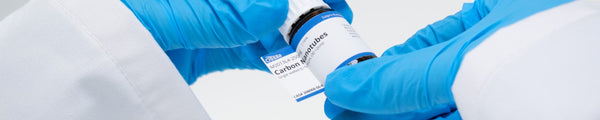
Learn More

Carbon nanotubes (CNTs) have unique properties such as high conductivity and strength. They have similar properties to another carbon allotrope known as graphene. This is due to the similarity in structure of 2D sheet-like graphene and 1D carbon nanotubes which are essentially cylindrical tubes of rolled up graphene.
Learn more...
Single-walled carbon nanotubes (SWCNTs) and multi-walled carbon nanotubes (MWCNTs) have some similarities and some key differences. Both materials are made from hexagonal lattices of carbon, specifically graphene sheets rolled up to form tubular structures. However, the nested structure of MWCNTs gives them distinct properties that differentiate them from SWCNTs.
Learn more...
References
- Functionalized carbon nanotubes: synthesis, properties and applications in..., Dubey, R., Nanoscale Adv. (2021)
- Carbon nanotubes: properties, synthesis, purification, and medical applications, Eatemadi, A., Nanoscale Res Lett. (2014)
- Single Walled and Multi Walled Carbon Nanotube Structure,..., Ganesh, E. N. et al., International Journal of Innovative Technology and Exploring Engineering (IJITEE) (2013)
- Carbon nanotube synthesis in a flame using laser..., Vander Wal, R. L. et al., Applied Physics A (2003)
- Large-scale production of single-walled carbon nanotubes by the..., Journet, C., Nature (1997)
Contributors
Written by
Application Scientist
Diagrams by
Graphic Designer