Deposition of Self-Assembled Monolayers (SAMs)


The deposition of self-assembled monolayer (SAM) molecules such as 2PACz is a critical process in surface science, nanotechnology, and material engineering. Like most organic or inorganic materials, the coating of SAMs onto substrates is carried out via various deposition techniques including:
- Evaporation Techniques - vapor-saturated environments
- Thermal Deposition
- Solution Processing of SAMs
SAM molecules can be incorporated with other materials to create hybrid solutions. This enhances the properties and functionalities of the resulting composite. Surface properties like adhesion, chemical resistance, and electronic behavior are often improved. Incorporation of SAM molecules can lead to advanced materials with tailored functionalities for applications in fields such as electronics, biotechnology, and materials science.
Solution Processing
Solution processing is by far the most convenient and widely used technique to coat self-assembled monolayers on a substrate (such as an ITO electrode). The deposition of SAM materials or hybrid mixture of SAM and perovskite materials can be carried out through solution processing. The most popular solution deposition methods include:
- Spin coating
- Spray coating
- Dip coating
Solution processing of SAMs can be broken down into several steps:
1. Substrate Preparation
The substrate must be clean and free of contaminants. For instance, gold substrates are often cleaned using techniques such as piranha solution treatment (a mixture of sulfuric acid and hydrogen peroxide) or plasma cleaning to remove organic residues. The cleanliness of the substrate is crucial as contaminants can inhibit the formation of a well-ordered monolayer.
2. Solution Preparation of Self-Assembled Monolayers
A typical concentration for different SAM molecules:
SAM Molecules | SAM Molecule Concentration | Solvents | Application |
---|---|---|---|
Alkanethiols | 1-10 mM | Ethanol, Hexane | Chemically resistant layer |
2PACz, MPA-CPA | 1 mM - 1 mg/ml | Ethanol, Isopropanol (IPA) | Hole selective contacts |
The choice of solvent depends on the solubility of the SAM molecules.
3. Solution deposition
The said solutions are then deposited onto the desired substrates via:
- Dip Coating
- Spin Coating
- Spray Coating
4. Annealing (Optional)
In some cases, the monolayer is subjected to thermal or chemical annealing to improve the ordering and packing density. Annealing can be performed by heating the substrate in a controlled environment or by exposure to solvent vapours.
5. Rinsing and Drying
The annealed substrate is then rinsed in most cases by spin coating with clean solvent to remove any non-adsorbed molecules, and dried under a stream of inert gas, such as nitrogen.

Spin Coating
Self-assembled monolayers are directly deposited onto a substrate which is typically a glass or silicon wafer. The desired substrate is positioned on a spin-coating apparatus. The SAM material suspended in an appropriate solvent is added to the substrate surface. The substrate is then spun at high speeds from hundreds to thousands of RPM for a specified duration.
During spinning, centrifugal force spreads the solution uniformly across the substrate, leading to the formation of a thin film. The solvent evaporates during spinning, leaving behind a solid film of self-assembled monolayer materials.
Post deposition annealing may be performed to improve the electrical conductivity and structural integrity of the film. Annealing conditions such as temperature and duration can be optimized based on the specific requirements of the application. Solvent treatment of the coated films can also be carried out by spin coating the coated film with the pure solvent.
A typical procedure involves 30 - 100 uL of self-assembled monolayer material solution (1.0 mg/ml in THF, DMF, IPA, ethanol, methanol, or a mixture of DMF and IPA) is deposited onto the centre of the substrate surface and spin-coated for 30 s at the speed of 3000 rpm. Then the coated substrate is annealed for 10 min at 100 ℃.
Advantages | Disadvantages |
---|---|
Simple Scalable Achieves uniform films over large areas |
Large material waste |
Dip Coating
A clean substrate is immersed in a solution containing self-assembled monolayer molecules. Immersion time can range from a few minutes to several hours, depending on the desired coverage and the nature of the molecules. During this time, the molecules in the solution spontaneously adsorb onto the substrate and self-organize into a monolayer.
Dip coating is a simple and cost-effective method for depositing thin films.
Spray Coating
Spray coating involves spraying a fine mist or aerosol of the polymer solution onto the substrate surface. Additional curing or annealing steps may be employed to enhance film properties such as adhesion, conductivity, and stability.
Spray coating offers advantages such as scalability, versatility in coating complex geometries, and minimal material waste. It is suitable for coating large area substrates and can be combined with masking techniques for selective deposition.
Achieving strong adhesion of the SAM to the substrate can be more difficult with spray coating compared to other deposition methods like immersion or spin coating. For applications requiring multiple layers of different materials, spray coating each layer uniformly and without contamination can be complex and challenging. The technique can sometimes result in a rough surface finish, which may not be desirable for certain applications that require ultra-smooth surfaces.
Advantages | Disadvantages |
---|---|
Good for fragile, irregular or oversized substrates Scalable Less material waste |
Adhesions issues Rough surface finish |
Evaporation Techniques
Evaporation techniques have also been popular with the deposition of self-assembled monolayers onto different substrate, especially irregular shaped substrates. Evaporation includes both vapor processing by exposing the substrate in the SAM vapor environment and vacuum deposition.
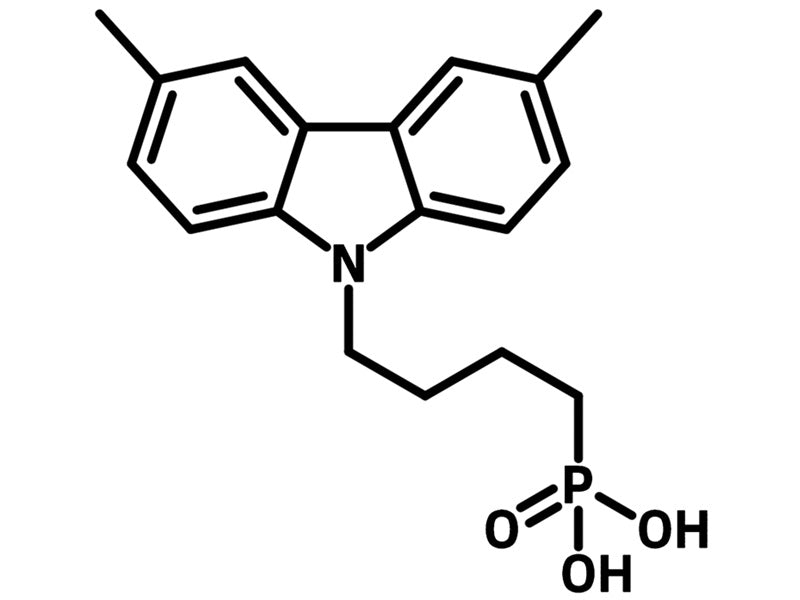
Vapor Processing
Vapour processing is suitable for SAM materials that are volatile. The SAM molecules are placed in a container and heated to produce a vapor. The specific temperature depends on the volatility of the precursor.
The substrate is placed in a vacuum chamber to reduce the presence of contaminants and improve the quality of the SAM. It is then exposed to the atmosphere saturated with those SAM molecules. Self-assembled monolayers form as the molecules condense and adsorb onto the surface of the substrate. Excess molecules and any by-products are removed by purging the chamber with an inert gas or applying a gentle vacuum.
Vacuum deposition methods involve the same thermal evaporation of SAM molecules but under vacuum. It is found to improve perovskite wetting to display conformal and high-quality coating of micrometre-sized textured surfaces.
Me-4PACZ is known to have a wetting and surface coverage problems. However, vapour deposition has achieved nearly 100% fabrication yield with high quality coating of micrometre-sized textured surfaces. As vacuum deposition is widely used in photovoltaic production, this makes it much easier to integrate into large scale production.
Self-Assembled Monolayers (SAMs)
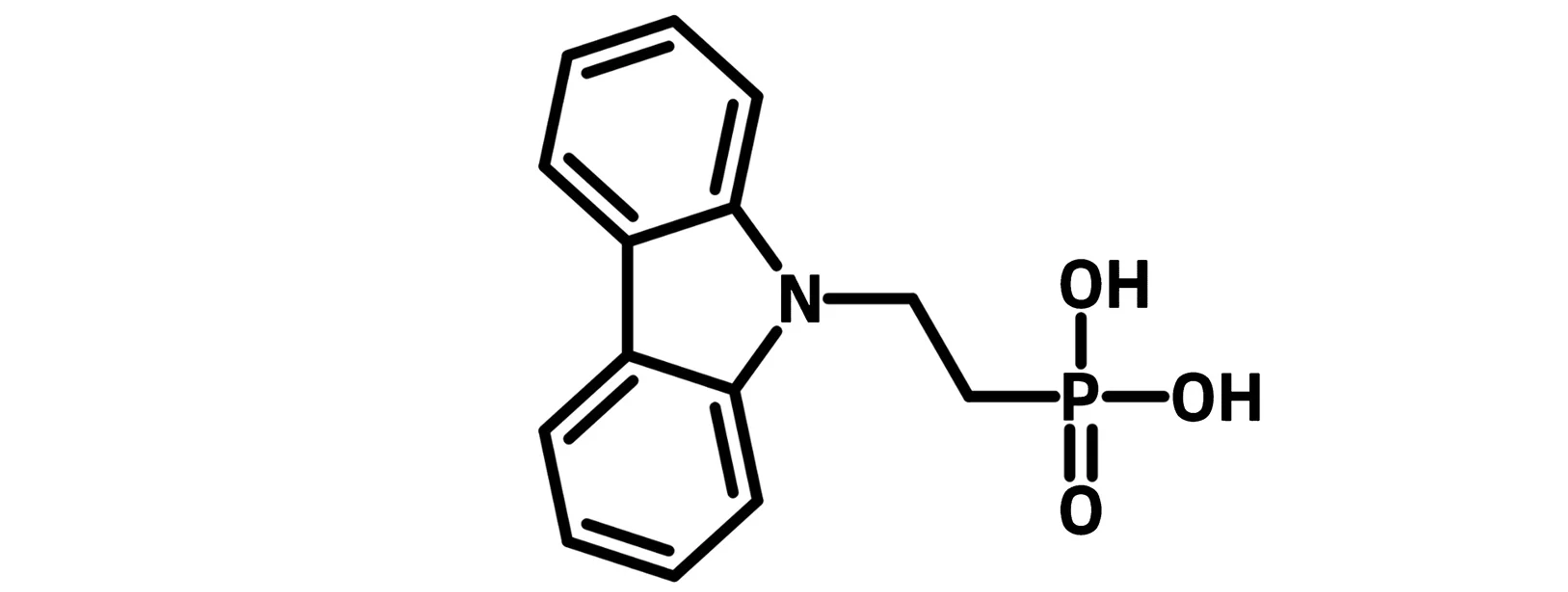
Learn More
Two commonly used materials for hole selective layer (HSL) or hole transport layer (HTL) are PEDOT:PSS (poly(3,4-ethylenedioxythiophene) polystyrene sulfonate) and self-assembled monolayers (SAMs). Each offers distinct advantages and limitations that impact their effectiveness in solar cells.
Read more...
Self-assembled monolayers (SAMs) are highly organized single layers of molecules that form on a surface. This is driven by the chemisorption of specific functional groups on the SAM molecules that have a strong affinity for a particular surface.
Read more...Further Reading
- J. Suo et al. (2024); The Dual Use of SAM Molecules for Efficient and Stable Perovskite Solar Cells, dv. Energy Mater., DOI: 10.1002/aenm.202400205.
- N. Gaur et al. (2024); Improved Thermally Activated Delayed Fluorescence-Based Electroluminescent Devices Using Vacuum-Processed Carbazole-Based Self-Assembled Monolayers, 9 (3), DOI: 10.1021/acsenergylett.3c02429
- S. Lee et al. (2024); Vacuum-Assisted Deposition of Highly Hydrophobic Self-Assembled Monolayer for High-Efficiency Perovskite Solar Cells, RLL Sol., DOI: 10.1002/solr.202400170