Micromanipulator Drift and Other Common Errors
Micromanipulators are precision instruments used to control tools or probes at a microscopic scale. A micromanipulator can be easily and precisely controlled to allow precision placement of electrodes or probes. However, their performance can suffer from various mechanical issues, including drift, backlash, side play, and sticking.
Micromanipulator Drift
Drift occurs when a micromanipulator or its probe gradually moves unintentionally over time, even without input or adjustment. This can result from:
- Thermal Expansion: Fluctuating temperatures can cause components to expand or contract, leading to slight positional changes. This is especially true for hydraulically controlled micromanipulators since the fluid (oil or water) has a higher volumetric thermal expansion coefficient than metals.
- Mechanical Relaxation: Over time, the materials used in the micromanipulator may relax, causing components to shift or deform. This could be due to poor construction, but it could even be simply the effects of gravity moving its positioning over time.
- System Instability: External vibrations or disturbances can destabilize the system, resulting in drift. For this reason, probe stations tend to have very elaborate vibration dampening supports or even acceleration-controlled hydraulic actuators to prevent vibrations caused by human interaction.
Drift can significantly compromise the accuracy of delicate manipulations, especially in long-term experiments or applications requiring precise positioning.
Backlash and Side Play
Backlash is the play or lost motion that occurs when the direction of movement is reversed. When a control input switches direction, there may be a noticeable delay before the micromanipulator begins to move in the new direction. This is due to mechanical clearances or tolerances in the drive mechanisms, such as gears or screws.
Backlash can hinder precise positioning and control, particularly during fine adjustments. It can lead to overshooting or undershooting the target position, reducing the overall accuracy of the manipulation.
Side play refers to unintended lateral movement of the micromanipulator or its components. This can occur when there is looseness or wear in the bearings, guide rails, or other mechanical components, allowing for unwanted movement in directions perpendicular to the intended motion.
This can compromise the precision of the micromanipulator, introducing errors in the positioning of the probe or tool. It can also make it difficult to maintain a stable position, especially during delicate manipulations.
Sticking
Sticking occurs when resistance or friction prevents smooth movement of the micromanipulator. This can happen due to:
- Friction: Friction between moving parts can impede smooth motion, particularly when components are not properly lubricated or aligned.
- Mechanical Binding: Misaligned components or debris can lead to binding and sticking.
Sticking can result in jerky or uneven movement, making it difficult to achieve fine, controlled manipulations. It can also lead to overshooting the target position and reducing the overall precision of the device.
Minimizing the Impact of These Issues
There are some things you can do to mitigate these effects. By understanding the causes and effects of these mechanical issues and implementing these strategies, researchers and technicians can significantly improve the performance and precision of their micromanipulators.
Things to consider when choosing a micromanipulator:
- Use high-quality components: Invest in precision components with minimal tolerances and high-quality materials to reduce mechanical play and wear.
- Solid engineering design principles: A well-designed micromanipulator should implement mechanical strategies to avoid issues like these. These could include spring-loaded mechanisms, tight tolerance motion stages, and precision micrometres.
- Proper maintenance and calibration: Regular maintenance, including lubrication and cleaning, can help minimize friction and ensure smooth operation. Calibration can help compensate for drift and other errors.
- Stable operating environment: Minimize temperature fluctuations, vibrations, and other disturbances that can contribute to drift and instability.
- Careful operation and technique: Employ careful and deliberate control inputs to avoid excessive force or sudden movements that can exacerbate backlash and sticking.
Ossila Micromanipulator
Elevate your microscopic manipulations with the Ossila Micromanipulator. Years of precision engineering and experience with sub-par probe stations have gone into its development. Our engineers have implemented solid design principles to avoid potential movement issues from the start:
- Each movement axis is spring-loaded against precision micrometre heads to prevent drift and backlash.
- The heavy-duty precision linear rails and bearings ensure superior accuracy and longevity by minimizing side play and sticking.
- The precision-milled aluminium body offers a lightweight yet stable platform with a low coefficient of thermal expansion.
On top of that, it is ergonomically designed for comfortable use and affordably priced to be accessible to as many labs as possible.
Micromanipulator

Learn More
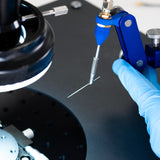
Learn how to accurately adjust your micromanipulator probe.
Read more...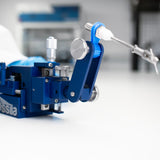
This guide gives an overview of how to use the Ossila Micromanipulators with the Source Measure Unit, as well as some general tips and tricks for getting the most out of sensitive electrical probing measurements.
Read more...Contributors
Written by
Product Developer
Diagrams by
Graphic Designer