Which Spin Coater Features Do I Need?
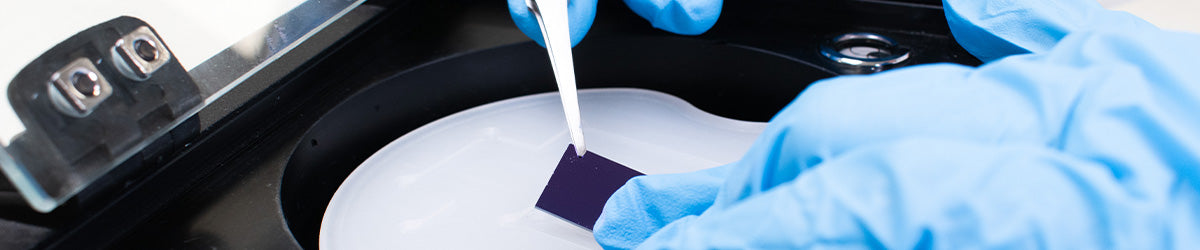
Other manufactures offer spin coaters with a range of advanced features. Depending on your application and scale of film production, these features can be both beneficial and damaging to your final films. Before investing in a new spin coater, it is crucial to consider the different features and specifications available in the market.
The Ossila Spin Coater is designed to be simple and effective for R&D and laboratory applications. We offer an affordable model that is optimized to last and create uniform films.
Purge Lines

Solvent vapours can erode the motor mechanisms, rubber gaskets, and other plastic components over time. The inclusion of purge lines can improve the lifetime of these components and the spin coater.
A purging gas is pumped into the motor housing at a slight over pressure. This pushes the gas from the motor housing, through the processing bowl and out of the lid. Solvent vapour is carried away out of the spin coater.
The processing environment is important and purge lines can help to improve film quality. For example:
- Purging with nitrogen can reduce the amount of oxygen in the chamber for air sensitive materials.
- Dry compressed air can be used to flush moisture from the chamber for processing moisture sensitive samples.
Disadvantages
Installing and maintaining purge lines within a spin coater significantly increases the overall cost.
Additionally, if not tightly controlled and managed, purge line can reduce film quality. Some spin coaters use a gas diffusing element to help evenly distribute purge gas through the processing chamber but they can introduce additional factors that can affect the process.
Do You Need Purge Lines?
A purge line can improve the lifetime of your spinc coater if it includes components that can be damaged by processing solvents. However, the lack of feedback on processing chamber conditions means you cannot optimize the use of purge lines.
If environmental factors need to be tightly controlled, common practice is to spin coat within a within a glove box, clean room, or fume hood.
Our spin coater uses a direct drive motor instead of a belt driven system, which is prone to damage from solvent vapours. The gasket materials are solvent resistant, which means the presence of the solvents are not detrimental to the lifetime of the motor. By utilising appropriate materials and design, we have eliminated the need for purge lines in the system.
Integrated Environmental Sensors
Spin coating is often done in ambient conditions where changes in humidity, temperature, and residual solvent vapour concentration can occur. Some materials require tighter control over atmospheric conditions.
Some spin coating systems integrate electronic sensors within the processing bowl. These can measure temperature, pressure, humidity, and volatile organic compounds. Typically, sensors are combine with intergrated purge lines.
Without the need to maintain a large environmental chamber, these systems have a lower running costs. This is because input gas is only required when processing, and only flushes a very small volume of space.
Disadvantages
Integrated sensors increase the size and inital cost of the spin coater, which is not always a viable or accessible option.
Additionally, integrated sensors provide more weak spots which can easily malfunction due to solvent exposure. Importantly, although integrated sensors can provide some level of control over your environment, they are not as effective as a dedicated environmental control system.
Do You Need Environmental Sensors?
Integrated sensors in your spin coater can be useful if you require detailed knowledge about your processing conditions. However, lots of thin film materials can be spin coated in ambient conditions, so this tight environmental control is usually not needed.
Also, chuck spin coaters are compact and require no fixed set up. They can easily be operated in any environment, including inside a glove box, allowing a controlled environment without the price tag.
Heating Elements
Heat can be used to affect the properties of the final film. By integrating a heating lamp or stage, users can directly heat samples before, during, or after the spin coating process.
Integrating heating elements into a spin coating system allows greater flexibility in controlling the film formation, growth dynamics, and processing parameters. It allows users to enhance specific properties of thin films by adjusting the temperature and the length of heat exposure.
Disadvantages
With heating lamps, the indirect transfer of heat can be ineffective compared to direct heat transfer methods. If heat treatment is not necessary, it can result in long cooling times without much benefit.
Do You Need A Heating Element?
In most cases, drying mechanics can be adequately controlled using post-deposition heat treatments. This can be done very simply by transferring the substrate to a hot plate. A spearate hot plate is much cheaper and easier than incorporating heating elements into your spin coater.
Edge Bead Removal and Back Side Washing
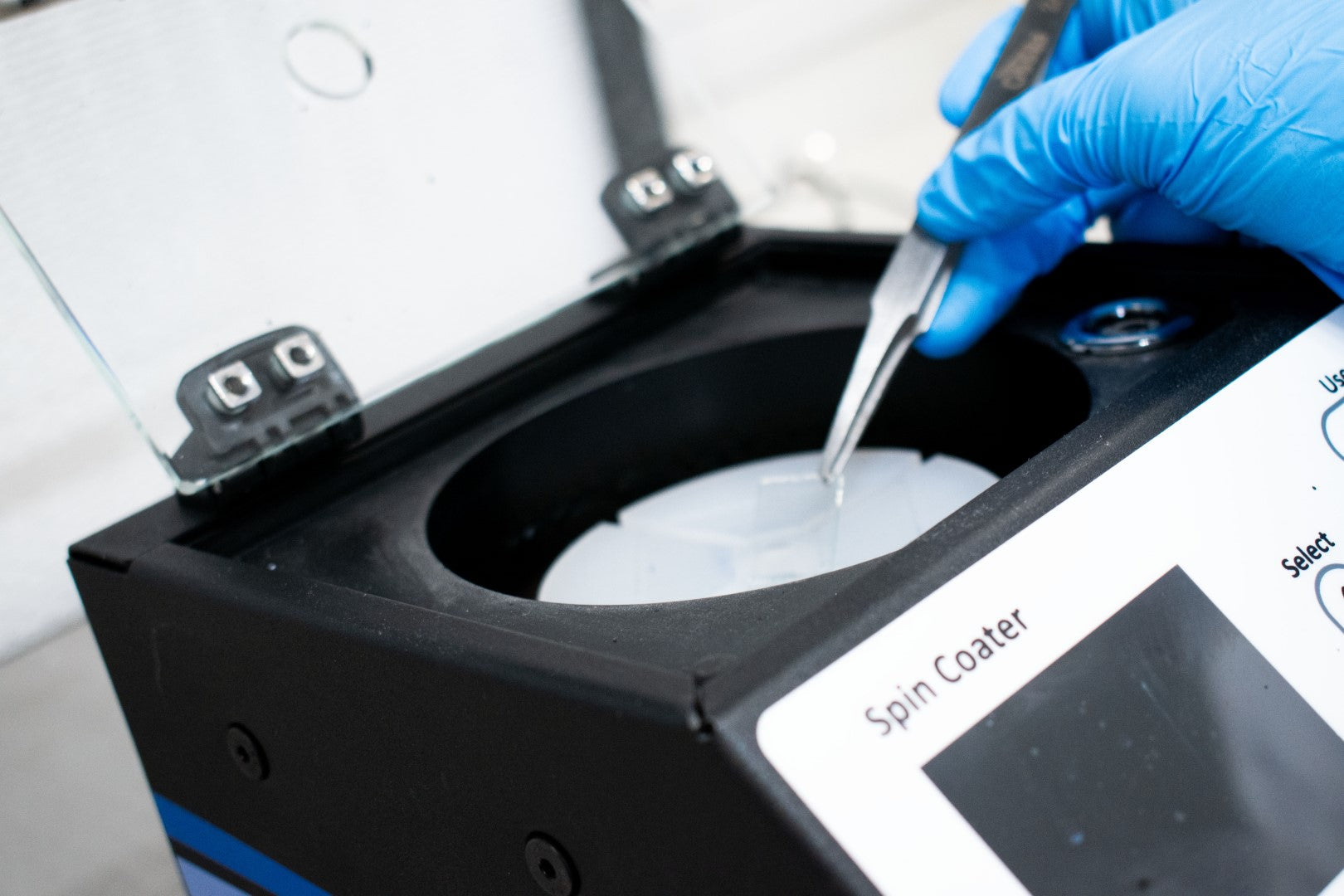
Backside washing prevents excess material from collecting on the underside of the substrate. A solvent is sprayed underneath to prevent material from gathering at the edge, which can distrupt photopatterning processes.
Edge bead removal prevents excess solid material forming at the edge of the dry film. A small stream of solvent is dispensed to counteract differences in drying rate across the substrate.
Disadvantages
At a small scale, both processes are difficult to control. The solvent itself can dissolve key areas of your film, reducing film quality.
Incorporating these features will increase the cost and size of your system. Additional maintenance is also needed and the system will require a long optimization process.
Do You Need Either?
These features are more prominently featured in large area or large scale wafer spin coating systems. These can be highly optimized with significant investment, as ensuring film uniformity is very important.
However in smaller area systems, these processes increase the potential for error significantly. In most cases, it is much easier to remove backside and edge layers manually once the spin coating process is complete. This way, you will not risk removing important material from your film.
Spin Washing
An intergrated cleaning system can prevent contamination of extremely sensitive materials. Spin washing floods the surface of the substrate with cleaning solution.
Dirt and dust contamination can be removed by providing a constant stream of cleaning solution and agitating the surface with constant acceleration.
Incorporating a cleaning process eliminates the need to transport the substrate, reducing the chance of contamination post-deposition. Reducing defects is important for manufacturing processes where the presence of defects needs to be minimized.
Disadvantages
The initialy cost of the system is higher than simpler spin coaters. Typically, spin washing requires additional drying elements, which can also increase costs. There is also an increase in maintenance as the cleaning solutio needs to be supplied and drained.
Unfortunately, spin washing cannot proved the same level of clanliness as manual cleaning.
Do You Need Spin Washing?
Spin washing is only necessary for large scale, highly optimized, highly sensitive procedures. For small scale R&D or laboratory experiments, the impact of delays between cleaning and deposition are minimal.
Additionally, the increased cost and upkeep of this system is not worth it where individual substrate cleaning can be done.
Choosing a Spin Coater
To choose the right spin coater model for your experimental needs and applications, it is helpful to consider the different features available across models and manufacturers. Features such as heating elements, edge bead removal, and purge lines can be advantageous in specific applications but still have challeneges and disadvantages.
Our spin coater includes necessary features such as a control system, range of speeds, and durable materials. We have designed the system to produce high-quality films while remaining affordable.
Spin Coater
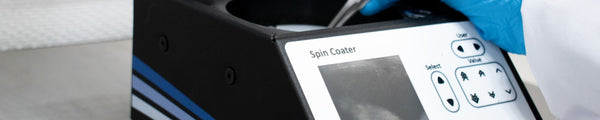
Contributing Authors
Written by
Product Developer
Edited by
Application Scientist