Getting Started with the Ossila Dip Coater
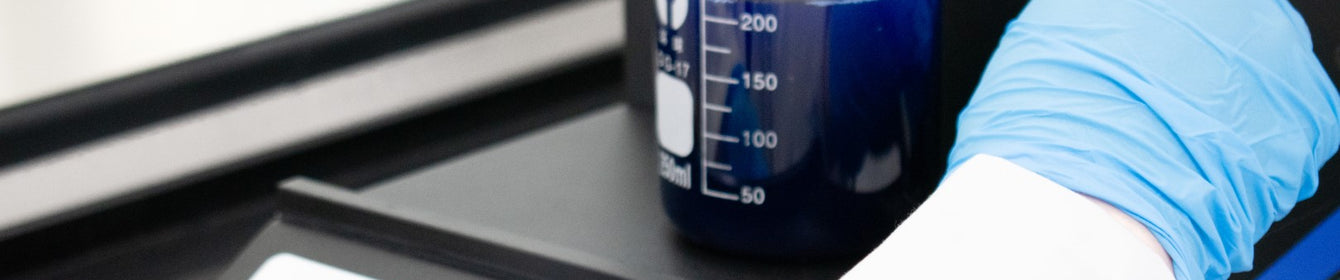
Dip coating is one of the most widely-used coating processes in industry and academia for producing thin films. To create a film, the substrate is first lowered into, and then withdrawn from, the solution. By controlling the speed of substrate withdrawal from solution using a programmable dip coater, you can vary the thickness of the deposited film. A high-precision motor means that the rate of withdrawal - and therefore the film thickness - can be controlled with a high degree of accuracy and reproducibility.
Because dip coating is suitable for roll-to-roll processing, it is used extensively in manufacturing. The Ossila Dip Coater allows researchers and academics to use the method in the lab. Dip coating is a straight-forward way of producing thin films, and it is therefore relatively easy to create high quality uniform coatings with little prior knowledge.
Dip coating theory
Dip coating utilises the behaviour of the solution meniscus, at the withdrawal point of the substrate from the solution bath, to control the thickness and properties of the deposited film. The interaction between the gravitational force acting on the withdrawn solution, the capillary forces of the solution, the surface tension, and inertial forces ultimately determine the amount of solution deposited onto the substrate. Although there are many factors involved in determining the strength of these forces and how an equilibrium between them is reached, almost all of these are constant for a given solution.
More information on the theory of dip coating can be found in our dip coating theory guide.
Dip coating film thickness equation
The thickness of the films formed during dip-coating is most closely given by the Landau-Levich equation.
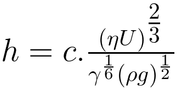
The values c, ρ, γ and η are properties of the deposited solution; where c is a constant that is dependent upon the behaviour of a solution, ρ is the density of the solution, γ is the surface tension at the liquid-air interface, and η is the viscosity of the solution. The value g is the gravitational constant and U is the withdrawal speed.
Please note that in practical circumstances, these equations do not give completely accurate theoretical determinations for thin-film thicknesses. This is because the exponent of the withdrawal speed can vary due to solution properties. When trying to optimise the processing conditions, calibration curves should be taken for the solution in use.
Our dip coating theory guide includes more details on the theoretical thin-film thicknesses, the interaction of the capillary and gravitational forces, and behaviour of the wet film during the withdrawal and drying phase.
Applications of Dip Coating
Dip coating can be used in a number of applications, including:
- Self-Assembled Monolayers
- Sol-Gel Coatings
- Thin-Film Electronics
- Protein Coatings
- Gas Sensing
- Microporous Foams
- Highly-Aligned Nanowire and Nanotube Arrays
- Oriented Crystallisation
Dip coating is especially well suited to research on protein coatings, protective coatings, and tribiological coatings. The method is an extremely versatile way of coating thin films on flat or tube shaped surfaces.
Dip Coater
