Doctor Blade Coating: Method, Coating Thickness and Design
Doctor blade coating (also known as blade coating) is a common technique used to apply a thin, uniform layer of solution onto a substrate. The process involves using a blade to spread a coating of solution across a surface.
The method is widely used across various industries including to coat paper and packaging, textiles, electronics and medical devices. It is a simple, versatile and easy-to-use technique that can produce thin, consistent coatings. This is essential for high-quality finishes for a range of products.
Factors such as blade height, angle, substrate, speed, and material viscosity are carefully controlled to achieve the desired coating properties. The technique is valued for its precision, scalability, and adaptability to different materials and applications, this makes it a critical process in both research and industrial production.
Doctor blade coating can be done manually or the process can be automated. An automated doctor blade coater moves a blade applicator at a set speed across a stage to create a uniform coating.
Doctor Blade Coater
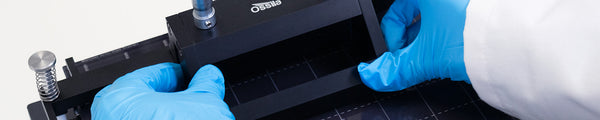
On This Page
- Doctor Blade Coating Process
- Doctor Blade Coater Design
- Doctor Blade Types and Materials
- Doctor Blade Angles
- Substrate Base, Holder or Tension System
- Solution Delivery and Control Systems
- Blade Coating Film Thickness
- Advantage of Doctor Blade Coating
- Doctor Blade Coating Disadvantages
- Doctor Blade Coating Applications
Doctor Blade Coating Process
The doctor blade coating process involves several key steps:
- Solution Preparation: Firstly, you must prepare the coating solution. The coating material, liquid or slurry must have the appropriate viscosity and consistency to ensure smooth application.
- Equipment Set-Up: The substrate and blade must be properly set up. Doctor-blade coating is compatible with many different substrates including: one or multiple smaller substrates, larger substrates, a continuous roll (web) or individual sheets.
Once the blade and substrate are properly aligned, the coating material is dispensed onto the substrate in front of the blade.
- Spreading and Smoothing: As the blade coater moves, it spreads the the coating material. The gap between the blade and the substrate will determine the film thickness. Other contributing factors to film thickness include the angle of the blade, the deposition speed and the properties of the coating material.
- Drying/Curing: After the wet film has been coated, the coated substrate typically undergoes drying or curing processes to solidify the coating. This curing can involve heat, UV light, air-blading or other curing method. The drying/curing method and the rate at which the solutions dries are both important factors.
Doctor Blade Coater Design
A doctor blade coating system consists of several components:
Doctor Blade Types and Materials
The blade is one of the most important parts of a doctor blade coating system. It is usually made from stainless steel, ceramic or plastic material. The choice of material depends on the required durability, resistance to corrosion and interaction with the coating material.
The blade edge can be sharp, rounded, or bevelled, depending on the desired coating thickness and the properties of the material being applied. The blade height (the gap between the blade and substrate) is adjustable, along with the blade angle, and applied pressure.There are various types of doctor blades.
The fixed blade is the most common type of doctor blade used. This is where the blade remains stationary at a fixed thickness from the substrate. This blade is ideal for precise and even coatings, such as thin film photovoltaics or electronics where film uniformity is important, where a set film thickness is needed.
Some printing systems use adjustable doctor blades. The flexibility is advantageous for applications which requrie different film thicknesses. With adjustable systems, you can vary this height without needing to change the blade. The ability to fine tune the gap provides versatility to industries who may specialise in flexible electronics or if coating different viscosities solutions.
There are also rotary blades, like those featured a rolling mechanism, which allow the blade to rotate as it moves across the substrate. This type of blade is advantageous where large scale coating applications are required.
If you are working with flexible or delicate substrates then you may choose to use a coating bar, such as a Mayer rod, rather than a flat blade. One advantage of the round design of a bar is that a more uniform pressure can be applied. A flat blade can create uneven pressure points accross certain substrates. A round bar is also less likely to damage to delicate substrates. However, bar coating thicknesses are less precise than with blade coating. As the cylindrical shape enables material to be spread evenly, bar coating is more suitable for thick coatings where high precision is not the priority.
Doctor Blade Angles
The angle at which the blade is applied is important as it has an impact on the thickness and uniformity of the final coating.
A perpendicular blade (90°) is an ideal angle for very thin, uniform coatings because it exerts the maximum shearing action. This means that the blade is positioned in such a way that it creates a shear force on the coating material, effectively restricting its movement and controlling the thickness of the layer left behind. This angle results with a very thin, uniform coating – making it a useful feature for applications such as precision optics or microelectronics.
At 45°, the blade creates a shear force against the liquid. This angle strikes a balance between removing excess material and allowing some material to stay on the substrate. However, this shear force still restricts the flow of the liquid underneath, meaning that only a limited amount of material can pass, which contributes to a medium thickness layer.
When a blade angle is situated between 15° to 30°, it is termed as a shallow blade angle, and these create thicker coatings by reducing the pressure on the material. You may want to use these angles for applications where larger material deposition is required or if you are working with highly viscous materials. Examples of relevant applications include battery slurries and the application of adhesive materials to substrates
Substrate Base, Holder or Tensioning System
The positioning and tension of the substrate must be precisely controlled to ensure uniform coating. The substrate must remain flat and aligned, preventing movement, wrinkles or deviations that could affect coating uniformity. The coater must be compatible with the type of substrate you wish to use, considering factors like the substrate's flexibility, thickness and sensitivity to pressure or heat.
Solution Delivery System
Some blade coaters have a reservoir to hold the coating material, helping to create a consistent supply. These are often more complex in large, automated systems, with sophisticated pumps and controls. In some cases, the material is directly applied to the substrate just before the doctor blade spreads it. In others, it may be applied via a secondary component, such as a roller. The choice of blade and other materials must be compatible with the coating material to prevent chemical reactions or wear.
Basic systems may use manual controls for all adjustments, whereas more advanced systems feature digital control panels or computer interfaces, allowing for precise control of all parameters and automation of the process. Automated systems often use internal software to control these parameters.
Automated vs. Manual Coaters
In manual doctor blading, the user manually controls the doctor blade, and therefore the coating process. Here, the user manually adjusts the blade height, angle, and applies the coating material. Automated doctor blading is a process that is controlled by automated machinery, for example computer-controlled systems which can control the blade and substrate movement, allowing users to automate their experiments.
Manual systems use screws to adjust the blade.Then the blade must be manually dragged across the substrate. Whereas automated systems use motors controlled by software to drive the blade across the substrate. This ensures consistent deposition speeds and leads to a more consistent thin film.
Some systems also feature blade height control mechanisms which will control of the gap between the blade and substrate.
Manual doctor blading is often used in early research and development, and other small-scale production. It is useful where flexibility and low cost may be the priority factors.
Automated doctor blade coaters are preferred in industrial and high-volume manufacturing settings where consistency, efficiency, and precision are critical to experiments. This system is common in industries like electronics, medical devices and large-scale paper and packaging productions. Automated systems are also preferred where reproducibility and consistency are the most important factors.
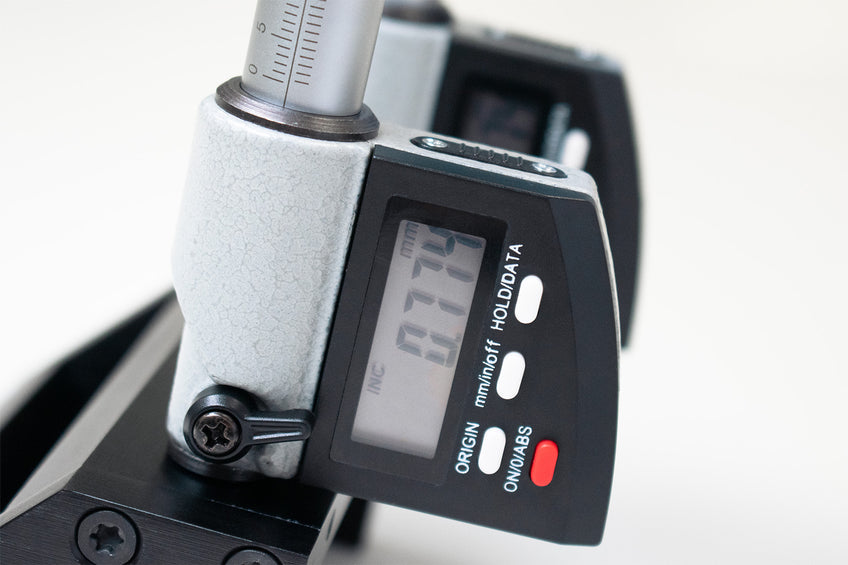
Doctor Blade Coating Film Thickness
Achieving accurate and consistent wet film thickness is crucial for achieving the desired properties in the final product, such as colour, conductivity, barrier properties and adhesion.

The formula describes a fundamental aspect of the doctor blade coating process: calculating wet film thickness. Wet film thickness is a critical parameter in ensuring that the coating meets the required specifications that you set for your experiments.
- Wet film thickness (h) – This is the thickness of the coating immediately after it has been applied to the substrate, before any drying or curing has occurred
- Flow rate (Q) – The volume of coating material applied per unit time, often measured in litres per minute (L/min). It represents the total amount of material being deposited in front of the doctor blade. This determines how much material is available for coating.
- Coating speed (v) – The speed at which the substrate moves relative to the doctor blade or vice versa. This speed is typically measured in metres per second (m/s).
- Substrate width (w) – The width of the substrate being coated, which is measured perpendicular to the direction of the coating movement. This width is often in metres or centimetres.
The formula essentially tells us the wet film thickness is directly proportional to the flow rate and inversely proportional to both coating speed and substrate width. In practical terms, this relationship should help in setting up the correct process parameters to achieve a specific coating thickness. Namely:
- Increasing flow rate (Q) will increase the wet film thickness, assuming other variables remain constant.
- Increasing coating speed (v) or substrate width (w) will decrease the wet film thickness.
You may need to adjust the flow rate, speed, or blade gap in a doctor blade coater to achieve a desired wet film thickness. Viscosity and surface tensions are also important properties to consider in doctor blade coating, because these properties of the coating material influence how it spreads and levels out once applied. Higher viscosity can lead to thicker films, however this might require more force to spread, while surface tension affects the smoothness of the film.
Blade configuration is also important; the angle of the blade, the force applied, and the blade’s flexibility can all influence the coating outcome. Adjusting these parameters can help control the thickness, uniformity, and smoothness of the coating.
Advantages of Doctor Blade Coating
Large Coating Area
Doctor blade coating is designed to quickly and reproducibly coat large areas with thin films. Most experimental research uses small quantities of materials coated over a small area, usually deposited using techniques like spin coating. After proof of concept experiments, the next most important stage of research to explore how scalable your processes are. This is especially true if your goals are related to real-life applications, such as producing new solar cell or battery technology or producing medical equipment or devices. Doctor blade coating can be an incredible tool to help you test the scalability of your materials or processes.
High Versatility
This technique can handle a wide range of coating materials with different viscosities and chemical compositions. Doctor blade coating is used to coat thin layers of slurries, liquids and pastes.
Quick, Reliable and Reproducible
With doctor blade coating, you can coat large areas very quickly. This is advantageous for high-volume production.
The simplicity of doctor blade coating make it a very reliable process. It is a well-understood technology. This helps to ensure reliable and repeatable results
Relatively Low Wastage
Doctor blading allows you to conduct your experiments with a reduced amount of coating material compared to other coating techniques. For example, dip coating which requires a large reservoir of excess material. Also, with spin coating 90% of the material applied is cast off as waste. With doctor blade coating, any excess solution after coating can be collected and filtered for reuse.
Easy to Use and Optimize
Compared to other large area coating techniques, such as slot-die coating, there is relatively few factors that need optimizing. You can vary your thickness simply by changing the blade you are using. Also, once you find a process that works it's incredibly easy to do this again and again.
Doctor Blade Coating Disadvantages
- Achieving uniform coatings can require precise set-up and calibration of the doctor blade. This, combined with the large coating areas, makes this more complex to optimize than say spin coating. Doctor blading technique is not as precise.
- Doctor blade coating is not suitable for coating extremely thin films. It is not possible to create films with thicknesses below 10s of microns for example.
- Coating materials with large particles or high solid content can cause issues like blade clogging or surface defects.
- Materials which have very low or very high viscosities can be challenging to apply uniformity, limiting the range of usable materials
Doctor Blade Coating Applications
Doctor blade coating is a versatile technique widely used across both industrial and research settings. It allows for control over coating thickness, uniformity, and material deposition over large areas making it applicable to a range of materials and products.
Industrial Applications
Some of the common applications of doctor blade coating include in the printing and packaging industries. It is commonly used in the printing industry to apply uniform layers of ink, varnishes and protective coatings on paper, plastics and other substrates. This ensures consistent colour quality and durability in printed materials.
It can also be used to apply adhesives and coatings in laminating processes, which are critical in packaging to provide protective barriers and enhance appearance.
The doctor blading technique is also used to deposit conductive and insulating layers in the manufacturing of LCDs, OLEDs and touchscreens. Thin films of conductive materials are important for the functionality of these devices.
Industrial applications require strong quality control to ensure that the coating achieved meets the standards set, therefore monitoring film thickness, uniformity and surface quality is needed – often by using advanced inspection systems.
Research – Scaling of laboratory techniques
In laboratories, doctor blade coating is widely used to study thin film materials, these include polymers, composites and nanomaterials. Researchers use such techniques to explore new material properties, structures and applications.
A specific analytical technique where doctor blading is useful is in microscopy, where preparing uniform thin films is crucial.
It is important to consider that in laboratory methods, achieving the same level of uniformity and consistency may require advanced machinery and process control systems. Scaling up also means that users will have larger quantities of coating materials to manage, this could require specialised feeding systems and environmental controls. The purpose of this is to prevent contamination whilst ensuring a consistent quality.
Doctor Blade Coater

Learn More
Thin films can be created through a range of coating methods including evaporation techniques and solution processing methods. Solution processing techniques uniformly coat a substrate with a solution, which then dries to make a thin film. Uniform and reliable thin film deposition is essential for the development and manufacture of solar cells and organic light emitting diodes, or other semiconductor devices.
Read more...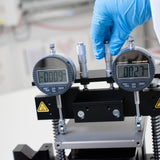
Bar coating is a simple wet processing technique used to deposit a thin layer of solution onto a substrate. It involves a bar being placed above a substrate and dragged over a pool of fluid, resulting in the fluid being spread into a thin film or coating. Bar coating is commonly used in the development of applications such as automotive paints, photovoltaic cells and lithium ion batteries.
Read more...