Why are OLEDs Expensive?
Following the development of OLEDs in the 1980s, Sony introduced the first OLED TV in the mid-2000s. The 11-inch display was only 3mm thick, making it the thinnest TV around, but it cost an eye-watering $2,500.
Today, OLED TVs still come with a hefty price tag. They occupy a niche market and are considered an evolving product. Advanced features, OLED material availability, fabrication issues, and the blue pixel problem are among some of the factors that keep the price of OLED technologies so high.
Advanced OLED Technology
OLED technologies are used in emissive display panels, where each individual pixel is self-lighting. On TVs and smartphone screens OLEDs provide true blacks, vivid colours, and even flexible or curved displays.

Along with a unique set of advantages, there inevitably comes a unique set of problems. One major issue for OLED panels, particularly in the early day was that of burn-in.
Lots of research and expense has gone into solving this problem. Burn-in can now be resolved using a function called ‘pixel shift’. This feature shifts a static image regularly to prevent image retention on-screen. The image is moved, pixel by pixel, in small increments in all directions.
Advanced features that protect the OLED pixels increase the display lifetime but also leads to increased initial costs. As these features become more common place, in comparison to earlier models, the average price point has gradually fallen. Nonetheless, the relative price point of OLED displays remains higher compared to similar LCD and LED models.
Organic Materials and Electronics
Organic metals, like iridium and platinum, are used in OLED technology.
These materials are less common than the inorganic materials used in traditional LEDs, such as silicon. This makes sourcing and purifying organic materials for OLED technology a more expensive process. Alternatively, synthesizing OLED materials in the lab also drives up costs.
The organic materials can also be an issue when incorporating them into existing manufacturing processes that are setup for traditional silicon-based devices.
Supply and Demand
At present OLED manufacturing occupies a niche market where demand outweighs supply. There are major factors revolving around the core materials and design structure of OLEDs that need to be urgently addressed for production to meet mass market demand in the future.
Problems that impact OLED supply can occur across various stages in the fabrication process, even beginning prior to manufacture, including:
- Sourcing the core materials
- Designing the product
- Manufacturing
- Testing
- Packaging
These problems can either be external or internal to the OLED device. External problems include factors such as the presence of impurities and instability in the manufacturing environment. Internal problems can exist in the electrochemistry of the device itself, which has to be therefore subject to rigorous and costly testing to ensure quality standards are met.
Once made, OLEDs are readily subject to degradation. Determining the exact causes of this is hard to do and there are many factors at play. These problems have to be investigated through repeated and rigorous quality control testing that inevitably drives up costs.
The Blue Pixel Problem
Colour television is produced by combining the three primary colours of red, green and blue. In modern displays, each pixel is made up of three individual OLED devices.
With each consisting of millions of microscopic OLEDs, high energy efficiency and consistency in resolution is required across the entire structure to create a quality picture.
Each pixel colour ages and degrades at different rates. The colour blue is particularly unstable and this impacts the lifetime of the device, compromising its longevity.
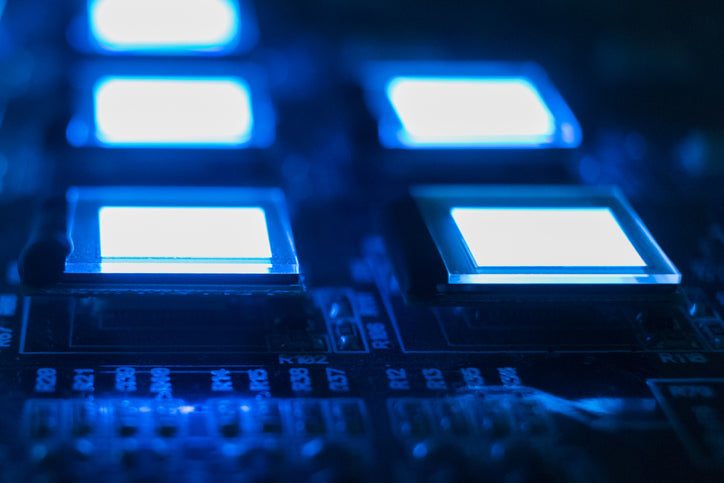
It is difficult to manufacture blue OLED emitters using next-generation processing methods. These methods involve solution-based processing, such as printing, instead of the traditional labour intensive, multistep vacuum-based methods. Traditional methods are costly and tend to produce lots of waste, so new processing methods are preferred.
Scientists are currently looking for ways around the blue pixel problem by searching for alternative materials and improving upon the design of OLED devices.
Structure and Fabrication
We can think of an OLEDs structure like a multi-layered sandwich. This structure evolved from a simple single structure because increasing the complexity was seen as necessary to improve the device efficiency. Yet, this complex structure has proven problematic to produce with newer, next generation solution-based manufacturing methods, like inkjet printing.
During production, a "stacking" problem can limit the efficiency of the device, as well as its longevity. Therefore, a very precise and costly process is required is required to achieve the best results.
As well as complicating the production process, complex multilayers add further problems too. Extra structural layers need additional supporting components. These extra components increase the amount of testing needed, increasing the cost of production.
Today, we are pressing the rewind button on the structure of OLED design. At the Max Plank Institute, scientists have recently worked on producing a single layered OLED. This would enable a blue emitter to be produced effectively by solution processing. If successful, this design could be mass produced and would lead to a reduction in costs.
Learn More
Additional Reading
Griffin, A. (2023) New OLED material breakthrough could mean cheaper OLED TVs. TechRadar. Online: https://www.techradar.com/news/new-oled-material-breakthrough-could-mean-cheaper-oled-tvs.
Sachnik, O. et al. (2023) Single-Layer Blue Organic Light-Emitting Diodes With Near-Unity Internal Quantum Efficiency, Advanced Materials, 35(26). doi. 10.1002/adma.202300574C
Schneider, C. (2023) New material concept allows more cost-effective production of blue organic light-emitting diodes. Physics.org. Online: https://phys.org/news/2023-09-material-concept-cost-effective-production-blue.html.